Hello everyone! My engineering capstone project is an analysis of vibrations in wheelchairs. What is the best way to approach this work using Altair?
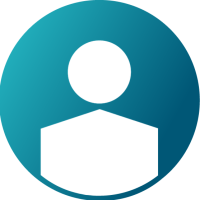
I would like to know if MotionView is the best solution for conducting the analysis. If I already have my 3D CAD parts completed, can I import these CAD drawings into MotionView, create the joints, and test vibration on a virtual road? Or do I need to use the Vehicle Tools to start modeling a half-car to simulate my wheelchair?
The main goal of the project is to determine if changing the wheel size can reduce the vibration on the wheelchair seat.
Best Answer
-
Hi Daniel,
There are several approaches to this project that you can take depending on the level of fidelity and the amount of time you have available, and MotionView will be the perfect tool for all of them. I would recommend completing our MotionView/MotionSolve Introduction v2023 eLearning to get the basics of Multibody Dynamics and MotionView before diving deep into this project.
All of the things you have listed above can easily be completed using MotionView:
- Importing CAD and attaching the Graphics to Bodies
- Creating Joints to add constraints to your model
- Simulating the model driving over a virtual road or on a shaker-post type system
Other topics to consider implementing into your model include:
- Converting frame pieces from solid bodies to FlexBodies
- Using FIALA tire models to capture higher fidelity tire-road interactions
My recommendation would be to create your own model as the assembly types from the Vehicle Tools Extension will not match a wheelchair well. Completing the Intro eLearning will give you the skills to complete this part of your project.
With regards to studying the effects of the tire, it will depend on what limits you have to your project:
- If there are commercial off-the-shelf tires that you are testing to see which is best, then you can modify an existing default FIALA tire model (from our installation directory) to represent the size, stiffness, and damping of the various available tires. Try to pick one that is closest to your goal size from our available models. Then you can use a NPOST event from the Vehicle Tools Extension to do a shaker-post simulation and measure the changes in acceleration at the rider seat for identical duty cycles.
- If there is no particular tire to replicate and you are just going to try different radii, then size may not actually make any difference. Typically, the wheelchair will have no suspension so all of the vibration inputs will have to be absorbed by the tire. If the stiffness and damping properties of the tire are kept constant but the radius of the tire is varied, then the results will likely be identical for all sizes.
If the goal of the Capstone project is to improve rider comfort, then I would also consider the addition of suspension elements like springs and dampers to help dissipate the energy coming in from the tire/road interface so all of the effort does not need to only be on the tires.
Hope this helps!
Adam Reid
2
Answers
-
Hi Daniel,
There are several approaches to this project that you can take depending on the level of fidelity and the amount of time you have available, and MotionView will be the perfect tool for all of them. I would recommend completing our MotionView/MotionSolve Introduction v2023 eLearning to get the basics of Multibody Dynamics and MotionView before diving deep into this project.
All of the things you have listed above can easily be completed using MotionView:
- Importing CAD and attaching the Graphics to Bodies
- Creating Joints to add constraints to your model
- Simulating the model driving over a virtual road or on a shaker-post type system
Other topics to consider implementing into your model include:
- Converting frame pieces from solid bodies to FlexBodies
- Using FIALA tire models to capture higher fidelity tire-road interactions
My recommendation would be to create your own model as the assembly types from the Vehicle Tools Extension will not match a wheelchair well. Completing the Intro eLearning will give you the skills to complete this part of your project.
With regards to studying the effects of the tire, it will depend on what limits you have to your project:
- If there are commercial off-the-shelf tires that you are testing to see which is best, then you can modify an existing default FIALA tire model (from our installation directory) to represent the size, stiffness, and damping of the various available tires. Try to pick one that is closest to your goal size from our available models. Then you can use a NPOST event from the Vehicle Tools Extension to do a shaker-post simulation and measure the changes in acceleration at the rider seat for identical duty cycles.
- If there is no particular tire to replicate and you are just going to try different radii, then size may not actually make any difference. Typically, the wheelchair will have no suspension so all of the vibration inputs will have to be absorbed by the tire. If the stiffness and damping properties of the tire are kept constant but the radius of the tire is varied, then the results will likely be identical for all sizes.
If the goal of the Capstone project is to improve rider comfort, then I would also consider the addition of suspension elements like springs and dampers to help dissipate the energy coming in from the tire/road interface so all of the effort does not need to only be on the tires.
Hope this helps!
Adam Reid
2 -
Adam Reid_21142 said:
Hi Daniel,
There are several approaches to this project that you can take depending on the level of fidelity and the amount of time you have available, and MotionView will be the perfect tool for all of them. I would recommend completing our MotionView/MotionSolve Introduction v2023 eLearning to get the basics of Multibody Dynamics and MotionView before diving deep into this project.
All of the things you have listed above can easily be completed using MotionView:
- Importing CAD and attaching the Graphics to Bodies
- Creating Joints to add constraints to your model
- Simulating the model driving over a virtual road or on a shaker-post type system
Other topics to consider implementing into your model include:
- Converting frame pieces from solid bodies to FlexBodies
- Using FIALA tire models to capture higher fidelity tire-road interactions
My recommendation would be to create your own model as the assembly types from the Vehicle Tools Extension will not match a wheelchair well. Completing the Intro eLearning will give you the skills to complete this part of your project.
With regards to studying the effects of the tire, it will depend on what limits you have to your project:
- If there are commercial off-the-shelf tires that you are testing to see which is best, then you can modify an existing default FIALA tire model (from our installation directory) to represent the size, stiffness, and damping of the various available tires. Try to pick one that is closest to your goal size from our available models. Then you can use a NPOST event from the Vehicle Tools Extension to do a shaker-post simulation and measure the changes in acceleration at the rider seat for identical duty cycles.
- If there is no particular tire to replicate and you are just going to try different radii, then size may not actually make any difference. Typically, the wheelchair will have no suspension so all of the vibration inputs will have to be absorbed by the tire. If the stiffness and damping properties of the tire are kept constant but the radius of the tire is varied, then the results will likely be identical for all sizes.
If the goal of the Capstone project is to improve rider comfort, then I would also consider the addition of suspension elements like springs and dampers to help dissipate the energy coming in from the tire/road interface so all of the effort does not need to only be on the tires.
Hope this helps!
Adam Reid
Hi, Adam!
Thanks for your response! It’s great to know I’m on the right track. I haven’t finished the eLearning yet, but once I do, I’ll start working on the model assembly in MotionView. I might reach out again if needed!
Thanks again!
0 -
Daniel dos Reis said:
Hi, Adam!
Thanks for your response! It’s great to know I’m on the right track. I haven’t finished the eLearning yet, but once I do, I’ll start working on the model assembly in MotionView. I might reach out again if needed!
Thanks again!
Hi Daniel,
Not a problem! We'll be here to help as more questions come up.
Thanks,
Adam Reid
0