3D Tensile Base on RD-3500
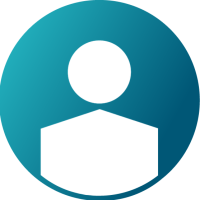

Dear all,
I've done with tutorial RD-3500 about tensile test & the result shows that the part is broken. And then I try to make 3D model of it problem and I use MAT23 & P14_Solid to the simulation.
The problem is, when I open the result in hyperview, my 3D model is not broken at ALL (see the attachment). What's wrong with my model?
Please help me. Thank you
Best regards,
Iron_Man
Note : If you need the .HM file, please message me.
Answers
-
Hi,
In the RD-3500 tutorial we have used /MAT/LAW2 and the failure parameters are provided for the material, which is Failure Plastic Strain is given as 0.75. When the plastic strain of the elements reaches the failure plastic strain value of 0.75, those shell elements will be failed and will be deleted, and the model is broken. Similarly, failure parameters should be set for /MAT/LAW23.
If you have set the failure parameters for /MAT/LAW23 and when the elements reach the failure criteria, for solid elements, the deviatoric stress of the corresponding integral point is permanently set to 0, however, the solid element is not deleted and so a broken like effect will not be visible for solid elements.
0 -
Dear George,
Thank you for your explanation,
I have set the value of failure plastic strain in MAT/LAW23 same with MAT/LAW2 (see attachment).
So, if I want to se my model is broken like in RD-3500 tutorial, what should I do? Change MAT type? or another step?
Thank you,
Best regards,
Iron_Man
0 -
Hi,
Please share the model file.
0 -
Hi,
Sorry for late reply,
For model file, please see attachment.
Thank you,
Best regards,
Iron_Man
0 -
Hi,
For Material Law 23 the solid elements are deleted when Epsmax (Failure Plastic Strain) value is reached. The max plastic strain developed in your model (as in the pic above) is .09 and the Epsmax value given is 0.75. And so, the elements will not fail. Reduce the Epsmax value within the range of maximum plastic strain value and try running the same.
0 -
Hi,
Thank you for your explanation, but let me know which parameter said 'The max plastic strain developed in your model (as in the pic above) is .09' ?
Because I don't see '.09' value in my picture above.
And from your explanation 'Reduce the Epsmax value within the range of maximum plastic strain value and try running the same', is there any suggestion how much Epsmax that should I use? or only with our intuition only?, because I never seen the equation or suggestion value to use.
Thank you very much.
Best regards,
Iron_Man
0 -
-
-
Thank you for your explanation.....
Yes, EPS_Max value is same between testing and FEM simulation....
But, I'm still don't understand on how to set EPS_Max Value as my question above.
Now, I'm still running new simulation base on your suggestion to reduce EPS_Max, and I set the value to 0.725. I will update the result if the simulation is finish.
Thank you,
Best regards,
Iron_Man
0 -
Hi,
Simulation with new condition (EPS_Max : 0.725) has been finished & the model still in solid condition, no break at all. (please attachment)
Thank you.
Best regards,
Iron_Man
0 -
HI,
In this case, you can see the results from HyperView. The plastic strain value is 9.241e-2 and you provided the failure plastic strain (Eps_max) value as .725. Only when then the plastic strain value reached 0.725, it will fail and those elements will be deleted.
I gave a plastic failure strain value of 0.07 and you can see the elements failing. Please find the attached image.
0 -
-
Hi,
Seems strange
Please check the attached files for reference.
0 -
Hi George,
Happy Monday....
Ok, I will check your files.
Thank you for your advise.
Best regards,
Iron_Man
0 -
I've reviewed your files & I didn't found something different.
I also have tried to modify the EPS_dam to the same value with EPS_max, and I got nothing.
Any other idea to check what's happening with my model?
Thank you & Best regards
Iron_Man
0 -
Hi,
The damage appears in the material when the strain is larger than a maximum value Eps_dam. Recommend you to refer the theory manual of RADIOSS (available in Help Menu) to know more on this material law. I have only modified the Eps_max value in the material card which is the failure parameter.
0