Combined topology and free size optimization
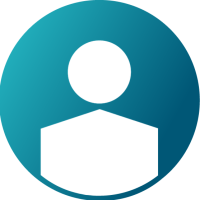

Hello all,
I would like to set up a combined topology and free size optimization. Okay, here is what I would like to do in more detail:
My initial design space is a cylinder with a 3 mm thick wall.
First, I want to optimize my part with the objective to minimize compliance and the constraint of a maximum volume fraction of, let's say, 30%. Like this, I get the main directions of stress and I see where material has to be. Since the material is pretty thin in the first place, it only takes material away and if I compare the deformation of the original part with the optimized part, of course, I get higher deformation values for the optimized part because there is less material. Therefore, step two:
Now in this second step, I would like to take this optimized structure, turn it into a shell, increase the shell thickness T to 6 mm and perform a free size optimization with the objective of minimizing the volume and two displacement constraints. One for torsion and one for bending.
I'm imagining an optimized structure, where I have a thicker wall, where the material is really needed to fulfil my deformation constraints and maybe thinner walls, where the stresses are not as high.
I tried to use OSSmooth to turn the resulting part of step 1 into an IGES geometry and then use auto midsurface to turn it into a shell. However, auto midsurface does not recognize the part as a solid and therefore does nothing at all when I want to create the midsurface.
Just performing step 1 with a thicker wall also doesn't work, since the loads on the part are comparably small and I don't get reliable optimization results when I add even more material in the design space. To illustrate how small the loads are, I calculated by hand how much material I could theoretically remove before the material will enter a plastic deformation. I could remove 90%.
Thank you very much for your help!
Best,
Chris
Answers
-
Hi Chris,
Can you try exporting as stp instead?
0 -
Yes, I tried. I tried with H3D as well out of desperation, but nothing worked. Maybe my export settings are not correct? I left most of them at the preconfigured values
0 -
-
Hi Chris,
Is it possible to share the file?
0 -
Yes, I'll upload it to your FileTransferLink in a second.
0 -
Hi Chris,
I suggest you to use a dedicated CAD tool to create a continuous surface/solid and import the same in HM for further pre-processing. It will take more time for editing and merging the solid blocks than using a CAD tool.
HM can do some basic CAD editing but not like a CAD tool.
0 -
Thank you, Prakash, for looking into my problem. I was hoping for a fast and convenient way to reanalyse the model, but I feared that this is not possible.
I will rebuilt the model in Catia then and set up a fresh optimization.
0 -
Chris,
I understand, but it will be a time taking process with HM to merge solids and extract mid surface.
It would be easy for you if you use any CAD tool to import the stp file and merge solids in the same.
0 -
That's the plan.
Thanks again, Prakash!
0