Error executing AcuSolve
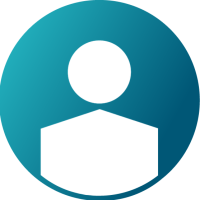

Hi everybody,
I’m new to AcuSolve. I have to do a CFD analisys (steady state) of a cooling fan of a coaxial pumping unit (the fan of a piston compressor), but i don’t understand why the analisys doesn’t reach the convergence and it finisches after several step (462) with an error (“error occured executing AcuSolve”). I have considered more inflow sections and more outflow sections, and the fluid inside the control volume is divided into two parts, a part around the fan (to assign the reference frame) and the part inside the carter (the control volume is a portion of the carter of the compressor).
I exported the model from hypermesh to acuconsole, and in acuconsole i set the following parameters:
• Analysis type: Steady State;
• Flow equation: Navier Stokes;
• Turbolence equation: Spalart Almaras;
• Fluid: Air (I left the default parameters for the air)
• At the fan i assigned a wall condition
• Reference frame (2850 rpm) assigned to the fan wall and to the fluid modelled around the fan
• Max time step= 1000;
• Convergence tollerance =0.01 (looking at the residual ratio i’ve seen that it doesn’t fall under 0.1)
I want atmospheric pressure in the inflow and outflow section, so in the “Simple boundary condition” i set pressure=0.0 N/m^2 for inflow and outflow(i suppose that 0.0 is the atmospheric pressure) and i’m interested to calculating the mass flux at the outflow.
This is the first time that i do a cfd analysis and it’s problably completely wrong, so i would be really happy if you helped me. I suppose that my mistake was to consider two different fluid in the control volume (two different geometry), and give to one the reference frame, but i’m not sure.
I post the .hm and .acs files, thanks in advance
Best regards
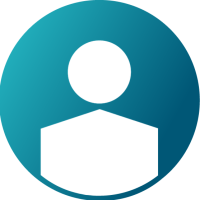

Hi raskolnikov,
Thanks for your answer, therefore i have to extend inflow and outflow section, but in this case i should set a 'slip' condition in the entrance and exit area and not a wall condition, so there isn't friction force and the air is free to slide on this 'artificial' Surface, isnt't it? Anyway i try to do the analysis in this condition and i let you know as soon as possible.
Best regards
Rather than having several inlet and outlet surfaces, you'll have better luck with a single inlet surface and a single outlet surface. The fluid will then be able to distribute appropriately to the various openings for the passages. It would be something like putting the fan inside a pipe or duct for the simulation.
You may also wish to contact your local Altair support office in Italy.
Hi arezzo95,
due to my experiences your case is strong turbulent, especially at the fan outlet, maybe at your inlet also if the back flows occur around the fan.
In this case I would build extensions for both, system inlet and outlet in order to get a fully developed flow on both sides. You can also create two interfaces, you dont have to seperate their names/parts, I mean: one fan inlet and outlet, to examine, for example fan inlet pressure or mass flow, ....
Best regards