Composite Tensile Test
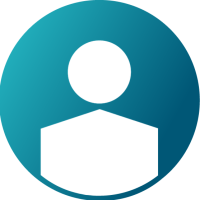

Hi,
I have encountered errors E11, E22, G12 not defined even though I have defined them. My purpose is to produce a stress-strain curve and mesh convergence curve out of the tensile test of 1mm/min rate. Please advice the appropriate solution for me to proceed.
Answers
-
Hi @Evan,
There are following problems with your model:
-'mesh' component should have card image set to Part
-MODULUS of E11, E22, G12, G23, G31 CANNOT BE EQUAL TO ZERO so you should also provide the G23 and G31 parameters. Also provide SIG parameters.
-empty shell element group IDs 1,6,7,8
-velocity vs. time function should be defined for imposed velocity
-I would also recommend some form of mass (AMS, DT/NODA/CST) and/or time scaling for computational efficiency
0 -
Hi Ivan,
Thanks for your quick response. However, I am simulating a plane stress and linear elastic composite condition, therefore dir 3 modulus is ignored. Do you have any recommendation of MAT LAW for stacked composite which is suitable for linear elastic condition? There is one MAT LAW, however, it is aimed towards isotropic material with only one Elastic modulus.
I am planning to extract quite a few things (ply stresses, general Exx and Eyy, stress-strain curve and mesh convergence curve) to validate the experimental data.
0 -
If your aim is to validate experimental data then you should have fully characterized material properties in all directions. Contact material supplier or look into the literature for missing parameters. If you are only interested in the elastic regime then yield stress can be set so high it does not influence the behavior in the linear elastic range.
You can try with LAW58 which can be defined without dir 3 modulus and yield stress, but is meant to simulate fabrics so it might not be appropriate.
Attached is the Composite Material, Property, Failure Model, and Element Type Compatibility for your reference.
0 -
Altair Forum User said:
Hi Ivan,
Thanks for your quick response. However, I am simulating a plane stress and linear elastic composite condition, therefore dir 3 modulus is ignored. Do you have any recommendation of MAT LAW for stacked composite which is suitable for linear elastic condition? There is one MAT LAW, however, it is aimed towards isotropic material with only one Elastic modulus.
I am planning to extract quite a few things (ply stresses, general Exx and Eyy, stress-strain curve and mesh convergence curve) to validate the experimental data.
In order to completely validate you can add more material details like allowable and type temperature dependent properties etc... Again, LAW25 deails with TSAI, CURSAV,
You can explore more material models like LAW 15, 27, etc...
0 -
Hi all,
Thanks for the reference pdf earlier. I have managed to get the RADIOSS engine to run the tensile test of using MAT LAW 25 and PROP P17 STACK (similar to PCOMPP) for my multiple-ply composite. However, the results don't seem to converge and it is taking a very long time to run considering this is just a shell. I couldn't figure what is the problem behind. Could you guide me on this ?
0 -
Hi,
Your model is better suited for implicit analysis. Explicit simulations take a long time to solve due to small timestep which is related to element length, stiffness and mass through the Courant–Friedrichs–Lewy (CFL) condition:
from Radioss free ebook:
<?xml version="1.0" encoding="UTF-8"?>
Also, the element size is so small compared to thickness it loses validity:
<?xml version="1.0" encoding="UTF-8"?>
So given the thickness of 1.6mm the element length should be around 16 mm
When h/L is large, shear deformation is at its maximum importance and the user should use solid elements. When h/L is small, transverse shear deformation is not important and thin shell elements are the most effective choice.
https://www.linkedin.com/pulse/shells-vs-solids-finite-element-analysis-quick-review-kuusisto-p-e-
0 -
Hi,
I see. However, increasing the element length will affect the contour during the post-processing. Regarding the simulation is more to implicit, I have looked through the large displacement tensile test tutorial in Optistruct. However, it seems to me that it overlaps with the experimental data to simulate. Any idea how to determine the tensile strength without coinciding with the experimental data ?
0 -
Mesh density and solution convergence are closely related and the factors which determine that relationship can be controversial. In an effort to meet specific time and accuracy requirements, trade-offs involving modeling time, accuracy, computation time, and cost must be made.
The correct mesh, from a numerical accuracy standpoint, is one that yields no significant differences in the results when a mesh refinement is introduced. Mesh refinements must accurately represent the problem in question if they are to be used in the analysis. Mesh refinements by simple splitting of elements can be misleading unless the newly created nodes conform closely to the original geometry. As refinement progresses, the original element selection must retain its significance. For example, a shell model can be refined to the point that it loses its validity in the area of interest, creating a need for a solid element model.
Please go through free ebook on Practical Aspects of Finite Element Simulation (a Study Guide) which can be downloaded from: http://www.altairuniversity.com/free-ebooks-2/free-ebook-practical-aspects-of-finite-element-simulation-a-study-guide/ . This contains all the basic theoretical concepts of Finite Element Analysis.
Actually, you need experimental data to validate a numerical model. Hyperstudy can be used to perform model calibration.
0