Model setup of composite curved structure for delamination fracture behavior
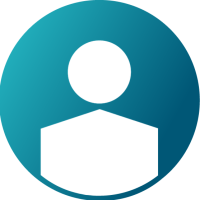

Hello Friends,
I made a ¼ symmetric 3D model for composite L-shaped structure to investigate the delamination behavior. The setup was as follows:
1) The unit: t-mm-s-MPa, Time: 1.2 s, Time frequency: 0.0012s, /AMS was used to reduce computation time. The velocity of the impactor is 20mm/s,
2) Interface Type 7 was used as contact, Igap= 0 to keep constant gap as same as Gapmin= 0.05.
3) Since I wanted to simulate delamination fracture process, I created Mat/Law 14. In the card, σt3 =55.6 MPa which is same with interlaminar tensile strength measured by the experiment,
When I checked the results of stress Z and Displacement-force curve as shown in attachments, the following disagreement with experiment was found:
1) According to the time-stress curves by creating /TH/BRIC/ card , when the maximum Stress Z is 44.28MPa , the delamination fracture behavior has occurred, however, σt3 is 55.6 MPa in the model. So what should I revise?
2) It takes me 2 days to calculate (workstation, options: -nt 64), but the oscillation still happened (The velocity of the impactor is 20mm/s), so how to modify the model that I can get the smooth curve by balancing the computation time and accuracy of results?
Besides, the force became zero after delamination because of separation between impactor and L-shaped specimen, however, in the experiment the force is not zero after delamination, so how to solve the problem?
Answers
-
Hi,
I recommend you to use /MAT/LAW12 than 14 (LAW12 is an improvement of LAW14 and more robust).
Is this a quasi static loading?.
If I understood well, the problem is that anim StressZ doesn’t show the correct behavior but the values output in TH are correct. Please recheck how the elements are oriented in the middle of the sample (where delamination appears) and also in which system the model is postprocessing.
You can try increasing the gap a bit (=0.5 if it’s possible).
Other way to do the same is using /FAIL/LAD_DAMA which uses the ladeveze criterion, so you’ll be able to set-up the damage kinetics.
0 -
Hi, George,
Thanks for your help. Yes, the loading condition is static one ( 2mm/min) in the experiment, and I set velocity as 20mm/s in the FE model to reduce computation time.
I modified my model with /MAT/LAW12 and increase the gap to 0.45 (Correspondingly set Gapmin as 0.4).
The element orientation is correct, and I solve the problem (maximum Stress Z is not equal to σt3 =55.6 MPa in the defined material card) by setting correct damage factors.
However, the problem ' 2) It takes me 2 days to calculate (workstation, options: -nt 64), but the oscillation still happened (The velocity of the impactor is 20mm/s), so how to modify the model that I can get the smooth curve by balancing the computation time and accuracy of results? Besides, the force became zero after delamination because of separation between impactor and L-shaped specimen, however, in the experiment the force is not zero after delamination, so how to solve the problem? ' is still not solved according to your suggestions.
So could you help me figure it out?
0 -
Hi,
The high computation time seems to be because of the time step drop.
From the engine out file user can find what is responsible for this time step drop.
- For an element, check the related material.There must not be an error in the units system that this data is given in. check the element size also.
- For a node, check the characteristics of connected elements. If the node is on the master side or the slave side of an interface, this interface must be verified.
- For an interface, the gap of the interface must be verified if some failure happens on the master or the slave side of the interface.
The other option is to introduce time step control using /DT/NODA/CST keyword. Ensure the mass error is less than 3-5% so that we can control the computation time without compromising the accuracy of results. The oscillations in the curve can be due to the dynamic effects in the model. You can also try with a higher value of /TFILE.
Can you please share the h3d file, through secure dropbox?.
0 -
Hi, George,
For speed the computation time, I have used /DT/AMS keyword, anyway, I just sent the h3d file to you, please check it.
Thanks very much.
0 -
Hi,
For the imposed displacement load try with a load curve gradually ramping up so that I think you can reduce the highly dynamic effects.
Also extract the damage parameters in h3d file.
I have a similar file with me which uses /FAIL/LAD_DAMA. Please go through the same attached, also through the engine file where control cards are used to extract damage parameters.
0 -
Hi, George,
Thanks for your suggestions.
1)Imposed velocity was used in the model, but high dynamic effects still occurred. So what should I do?
2)I checked your attachments, however, there is no information about how to extract damage parameters when we used /FAIL/LAD_DAMA keyword. BTW, I cannot find /ANIM/SHELL/IPLY/MAXDA, /ANIM/SHELL/IPLY/DAM keywords in the engine file in Radioss Block 140 which suggested in another post. For Radioss 140, can we extract damage parameters?
3)Besides, /FAIL/LAD_DAMA was also tried, it seems worked, at least for fracture stress, however, the results' animation look very weird. Please see the attachment. I have no idea what happened after delamination, so what should I do?
0 -
Does anyone help me solve the above problem?
0 -
Hi,
Please share your model file with the .h3d and T01 files through the secure dropbox, so that we can check and update you.
0 -
Hi, George,
I sent the files to you for your information, please check them.
Thank you very much.
0 -
Hi Gregory,
Delamination failure is a kind of separation of layers. If you review the model which I have sent you earlier, the layers are modeled with plies and laminates.
A similar approach you will have to try for this. You can try modelling multiple solid layers for this case.
0 -
Hi, George,
Thanks for help.
I am afraid that the model you sent to me was not same as what you said, because the layers are modeled using PROP17 and PROP 19 rather than creating plies and laminates. Moreover, I cannot find how to extract damage parameters by using /FAIL/LAD_DAMA in engine files of your model. Of course, if I misunderstand, please point it out.
Besides, in my case, which one do you recommend as follows?
1) Layers are modeled using PROP17 and PROP 19.
2) Layers are modeled by creating plies and laminates.
0 -
Besides, I checked the keyword /FAIL/LAD_DAMA, the 'help' files show that for Quad 2D element, only Mode II and Mode III are available. However, the investigation on Mode I was the focus even though 2D element was used in my case. So does that mean only multiple solid layers can be used to study the Mode I by using /FAIL/LAD_DAMA?
0 -
Hi,
For Mode 1 with Ladeveze failure model best is solids but should be modeled with multiple layers.
0