Energy Error decreasing
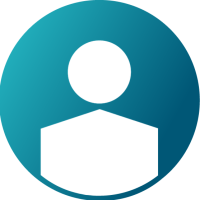

Hello,
I have a problem with decreasing negative energy error. I read the reason for this could be energy dissipation and the total error should not exceed 5-10% for a good model.
But in my case it reaches about -80 till -90% which indicates a wrong setup.
The model setup contains two steel rods with an elastomer buffer in between. I checked if the reason could be the material definition of the elastomer, therefore I assigned material parameters for steel to the buffer but the error is still decreasing like before. Additionally I unchecked the status of ENG_DAMP card to see if that's causing the error but it changed nothing either.
I don't know what else to check, so I'd be very grateful if you have a look at my model.
Answers
-
Hi MeshD
If you have included coefficient of friction then the energy error is due to coefficient of friction which is justified. If this amount of energy error is there when no coefficient of friction is defined, then it may be a case of penetration which is problematic.
Thanks
0 -
Hi Nachiket,
thank you for your fast reply. I didn't take account of any friction.
I checked the model for penetration. The tool returned no penetrations/intersections. Do you have any further suggestions?
Thanks
Edit: Is defining contacts mandatory for any simulation?
0 -
Hi,
Negative Energy Error represents energy dissipated from the system and this can be from many sources including plastic deformation and Hourglass energy.
Please check the hourglass energy of the model.Keep Isolid=24 and try running the simulation.
If the components penetrate each other due to the loads applied the user need to define an interface/contact between them for achieving a realistic simulation. The master segment can be parts, elements, contact surface, node sets and similarly for slave the selection can be parts and node sets. Once these master slave sets are identified the algorithm will check these locations for potential penetration of a slave node through a master segment, and this check is done in every time step.
0 -
Hi George,
changing ISOLID to 24 worked for me. Now the error stays at 0.0%
0