Carbon Fibre Tows Simulation in Hypermesh
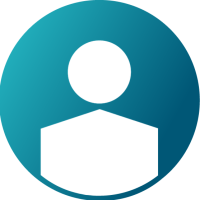

Dear Community,
my name is Lennart, I am a composites engineering student from Germany and I have started working with Optistruct/Hypermesh full-time since a few weeks. I am trying to get ahold of composite optimisation.
Optistruct is only partially able to compute composite parts. it appears that I am very limited in the design of more complex parts. What I am looking for in particular is a way to not only design plies in flat structures, but rather tows and roving in 3D parts, for example a scaffold of a crane or similar.
I AM able to model 3D composite structures by designing surfaces which come close to the 3D part and apply a laminate as a workaround.
As a first step towards 3D composite optimisation, I would like to have a workaround solution for working with single tows. For example if I have a 2D circular part, let's say a simple ring.
If I apply a tensile force (with a bolt or similar), the ideal optimisation result for a minimum displacement of the circle geometry would be a 'ring' of carbon fibres. However I am not quite sure how to get this result in Optistruct. This is not possible when the program only 'thinks' with plies.
is there any way how I could achieve this result with the given Optistruct possibilites? Any way to 'cheat' and work with single fibre tows instead of plies?
Any help would be greatly apprechiated.
Regards,
Lenny
Answers
-
Hi @Lenny
What type of optimization are you interested in?
How are you applying the forces in the circular ring?
Is it on the circumference or at the middle?
0 -
I am interested in finding the optimum ply lay-up for my complex CFRP part and I am trying to understand how to make Hypermesh/Optistruct do what I want it to do by starting off with simple geometries and working my way up.
Ultimately, I want my to optimize the topology of my part and have carbon fibres places ideally for all load cases.As for the ring geometry:
I am applying the force on the center of a Rigid Body Element (RBE2), which connects its centre node to all the nodes on the inner 'line' of the ring.
So I am applying the force at the middle.0 -
Altair Forum User said:
As for the ring geometry:
I am applying the force on the center of a Rigid Body Element (RBE2), which connects its centre node to all the nodes on the inner 'line' of the ring.
So I am applying the force at the middle.OK thanks. I will try to reproduce the a similar situation. Just another question. Is the force normal to ply surface?
0 -
No, the force is parallel to the ply surface, thus the force will only deform the ring and not bend it. The surface part (ring) and the force are parallel to each other in on plane.
Thank you for your effort!
/emoticons/default_smile.png' srcset='/emoticons/smile@2x.png 2x' title=':)' width='20' />
0 -
Hello,
If you don't mind me asking, have you come to a conclusion?
/emoticons/default_smile.png' srcset='/emoticons/smile@2x.png 2x' title=':)' width='20' />
0 -
I am working with free size instead of topology just to check the pattern. So far no success..
Let me explain what I have done so far...
1) 4 layers of plies
2) Applied a force in the middle on a RBE2
3) Cyclic pattern constrain used
Let me know if this is what you are doing...
0 -
This is exactly what I am looking for.
I used multiple plies with steps of 5°, to get a more accurate result, but this should work just as fine.The optimum result of the fibre orientation optimisation should be forming a 'ring' within the circular part, which, in reality, is the ideal fibre positioning.
However as mentioned, I am unsure how to achieve the expected optimum result. I am unsure if Optistruct is able to compute this case with realistic results.0 -
0
-
0
-
Oh my god yes, this is exactly what I expect the result to be!
Would you mind sharing with me how exactly you achieved this?/emoticons/default_smile.png' srcset='/emoticons/smile@2x.png 2x' title=':)' width='20' />
Thank you so so much!0 -
I applied a moment around the axis of disc. With load perpendicular to axis was not helpful at all. I attached the model file.
0 -
Wow! This is exactly what I was looking for!
if you don't mind me asking, how did you manage to make the 0° ply direction go in a circular manner?I can only get it to point into one global direction (x,y,z), but having the ply/material direction go in circles around the part should come quite handy!
Your support is amazing, thank you so much.
0 -
Create a cylindrical coordinate system. I assumed 0deg in the direction of radius and anything perpendicular will be 90deg which lays fiber in circular manner.
0 -
Perfect, exactly what I needed.
Thank you so much!/emoticons/default_smile.png' srcset='/emoticons/smile@2x.png 2x' title=':)' width='20' />
0