Material for very thin Shell elements
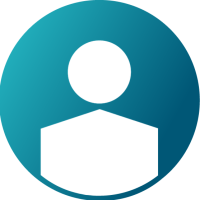

Hi All
My analysis contains thin plastic (thk=0.1mm) bag subjected to pressure.
I have results for 2
1.Optistruct static pressure analysis (100 KPa , used shell elements QUADR ,TRIAR,ELASTIC material )
2.Radioss Dynamic pressure analysis (0 KPa to 100 KPa varying over time , used shell elements SHELL4N ,SHELL3N , ELASTIC material)
but my stress values for Static (Optistruct) twice as for Dynamic (Radioss) are , but no clue.
my questions
1,have i used correct element /Materials for above analysis?
2.Since analysis id of very thin plastic elements , do i need use any other elements /material for Radioss?
Any help is much appreciated.
Regards
Kash
Answers
-
Hi Kash,
From my understanding I feel that this is an intended behavior of the simulation. In OptiStruct, it is a static case where load is applied where as in RADIOSS the load is ramped on to the model based on the load curve defined. Normally if we are looking for a steady state value, then the loads must be ramped up slowly. The load must ramp up from zero to the desired final value to get a steady state response.Based on the curve defined, the load will be applied to the model and the model will behave accordingly.
0 -
Hi George
Thanks for explanation.
Also i have below question
Also does Radioss has element type to represent membrane (a very thin elements)?
or
is there material type (i used M1_ELAST) to represent the membrane behavior?
Regards
Kash
0 -
Hi Kash,
To emulate a membrane element use only one integration point (N=1) for computation.
For an elastic material (Law 1) due to the analytical computation, the option is ignored. One way to get a membrane element with an elastic material is to use an elasto-plastic law (Johnson-Cook law) with a very high yield stress (for example: 1e+30).
0 -
Hi Kash,
What is the loading type i,e internal pressure or external pressure?
Also what is the ramp time used for the run in radioss?
Are the higher stresses coming near weld locations (are weld modelled by rigids) , in that case the near by elemental high stresses can be neglected I think.
0