Error #312
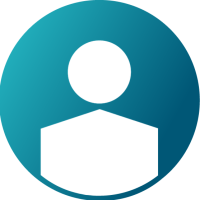

Hi, I have been getting this error and I have referred to other comments here as well, I have constrained my boundary constraints with respect to rotational dof well. I have one rbe2 element connecting the two components. Is it possible for anyone to tell what could be the actual problem?? I have attached the output file.
The compliance is negative or large 1.44361e+008.
The rotational displacement has a large magnitude, -183.872 degrees (larger than 180).
The rotational degree of freedom may not be constrained properly in the model.
subcase id = 1
grid id = 31
component = 5
Answers
-
0
-
Hi Prakash,
I recognized there were some mistakes with respect to the optimization parameters due to the ply thickness, but now I have removed it and I am still getting the same error, the thickness of the laminate is getting reduced uniformly and I don't seem to understand why I am not getting a difference in thickness. I am performing free size optimization. I am also getting an error for every 4th iteration and the mass in that case when I checked in the output file is really less and it is self-explanatory to me that the analysis would fail for a lower mass as such.
In my case, I want to reduce the volume such that the displacement in a node does not exceed more than a certain value. Thus I have given that value in the upper limit on the constraints. I have also kept the laminate thickness to the value between the thickness of the current model to the least value such as 0.05 for example. I have 1 pln symmetric pattern grouping.
I am getting the constant error that the object is undergoing rigid body motion after like the 4th iteration and sometimes the compliance is large. Could you tell me if there are any mistakes that could be possible in the model.
0 -
Hi @Adithya
Could you share the model files, please?
Please use the file transfer link in my signature to share the model file
0 -
Dear Adithya,
Please run an analysis before you run an optimization. Check the deflection of your model and check if the values are realistic.
If not, check your material parameters for the right units. This was the cause of the large deflection limit in my model.
So check your loads, boundary conditions and material parameters by performing an analysis. Good luck!
Regards, Michael
0 -
Hi Prakash,
I have attached the file in file transfer link
Thank you
0 -
0
-
Hi @Adithya
I have shared a file with you. Please try that.
Please have a look at the changes I made in responses and also the laminate bounds. I have made a rough assumption and provided the upper and lower bounds for laminate thickness.
You can change the bounds according to your requirement, but make sure that very small value will lead to failure.
0 -
Hi Prakash, Thank you for your guidance. Now i understand what the problem was.
for other readers if they face the same issue, the upper bound negative sign was the issue. The upper bound value set has to be negative if the displacement is acting in the negative direction.
0 -
Altair Forum User said:
Hi Prakash, Thank you for your guidance. Now i understand what the problem was.
for other readers if they face the same issue, the upper bound negative sign was the issue. The upper bound value set has to be negative if the displacement is acting in the negative direction.
Also the minimum laminate thickness constraint.
0