SIMSOLID: Why do we see jagged results if arbitrary shapes like a single part can be "finite elements"
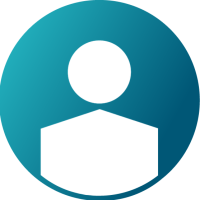
According to the white paper of Simsolid, volumes, areas, points, can be used as " finite elements" which implies that single volumetric parts can be a finite element.
Why then do we tend to see jagged stress results in different regions of the part, if the part is a single element? I am aware of CAD quality and using the most accurate CAD import settings etc.
Attached are some examples from Simsolid.
Answers
-
What do you want to compare? SimSolid vs Solidworks ?
For me, SimSolid is just only Conception tool, not really Finite Elements tool as Ansys or Abaqus.
0 -
Agree... it will never be a replacement tool for standard FEM methods, at least for now. However, it would be good to know what the tool is doing so that one can report with confidence to their peers.
I am just curious as to what is happening behind the scene with this tool (especially the jagged results). Appears to be very little info out there apart from the white paper and various benchmarking docs etc.
0 -
If I understand correctly, SimSolid uses p-method while traditional FEM softwares use h-method.
0 -
Ira, Nguyen,
SimSolid uses a meshless technique, to solve the FE problem. SimSolid does not use P element formulation.
For the display of the results, SimSolid uses a tessellated surface mesh on which it projects the results.It appears that the tessellation in this case is a bit coarse, thus causing the results to look choppy. We are going to enhance the behavior to avoid this artifact.
Whether you want to use SS as a concept tool or a complementary tool to your traditional FE suite will depend on the problems you are solving and the correlation to test or analytical solutions, that you are able to achieve. Correlating to other FEA codes is not necessarily the right approach.
1 -
Thanks for the update Chayan,
I believe SS uses different classes of functions to describe the displacement filed compared to the basic polynomial functions with h/p method. I wonder how much smaller the sub volumes are partitioned to apply the classes of functions?
That is interesting regarding the tessellated surface mesh for results mapping. That means in theory one could export this map for further calculations like fatigue with femfat?
0 -
this dependes on the number of passes and also the regions of your model. Areas where the is more variation tends to be "more refined/enriched" during the proccess, depending on the number of passes.
There is an option for importing specific coordinates into SS in order to request results specifically iin these coordinates.
This might really be useful for fatigue assessment.
1 -
I was disappointed to see that we cannot assess sub-surfaces stresses in Simsolid.... clipping only reveals results on the surface.
Perhaps in a future release?
0