This article provides an overview of Response Spectrum Analysis with theory and tutorial.
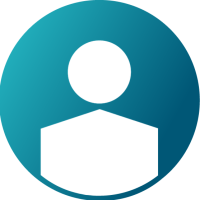
Alberto Campagna
Altair Employee

Response Spectrum Analysis
Introduction
Response Spectrum Analysis (RSA) is a technique used to estimate the maximum response of a structure to a transient event.
The technique combines response spectra for a specified dynamic loading with results of a normal modes analysis.
The attached .pdf discusses the usage of this method.
6