How to model blast furnace charging using EDEM
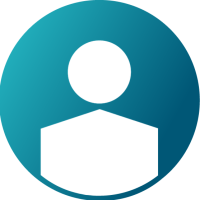

In this post we discuss the challenges of modelling a blast furnace using Altair® EDEM™. Simulation files with an example already setup can be downloaded here:
The Steelmaking industry is working towards reducing carbon emissions, with a goal of being as close as possible to carbon neutral. With governments and institutions setting goals to achieve “Green Steel” such as the 2015 Paris Agreement [1][2], making informed progress towards these goals is crucial.
Multiple challenges are faced by the steelmaking industry when it comes to optimizing and working with blast furnaces, these include:
- Physical Testing
- The size of the system, the chemical reactions, the opacity (black box) nature of the system and overall cost limit the options to do any full scale physical testing
- Material Segregation
- Non-optimal segregation occurring during charging, and during burden distribution, can significantly affect the efficiency of the furnace.
- This also negatively influences the molten/pig iron obtained from the process.
- Furnace maintenance
- Wear and abrasion on the staves and distribution chute can cause challenges and high maintenance costs.
Using EDEM, you can help resolve these challenges by modelling the charging of a blast furnace. Obtaining highly relevant information on the efficiency of the process from a virtual model. Allowing you to optimize the burden distribution and predict any segregation or wear on the distributor chute and wall staves, covering many of the challenges generally found in blast furnaces.
Step 1 - Set the material model
For this simulation a custom non-calibrated EDEM Material Model was created based on realistic values. However you could also use the GEMM Database as a starting point for your material, which would already be a good approximation and set the interaction parameters between the particles and the bulk material and equipment (after you select the friction level desired).
Material Models Libraries in EDEM
Step 2 - Material Calibration
Materials should be calibrated or use existing material models:
Discrete Element Method Calibration with EDEM
Step 3 – Import equipment from CAD
You can create your own equipment models in any CAD package and import it into EDEM, many file types such as STL, STEP, IGES to name a few, are supported. Geometries are imported to EDEM via the Creator > Geometries > Import Geometry section and will be by default meshed automatically unless the format imported already has a previously defined mesh. Generally mesh element size is not very important for DEM simulation results; however you may want to manually define the mesh definition if you want to do some wear analysis on the staves or distributor chute, as this will give you a more detailed wear pattern.
Step 4 – Introduce Material
The material in the example attached to this post is already generated. However, you could create your material with a dynamic factory that fits inside of the silo or even fill the silos in a prior simulation with the chute or conveyor system that fills them. Once they were filled you could save the silos as material blocks that could be imported into the charging simulation to introduce all the material already in the silo with the correct segregation and position of the material based on the filling.
Step 5 – Assign Kinematics
You can assign different types of motion to the geometries, but in a blast furnace with a distributor chute only one kinematic would be required. This would be a Linear Rotational Kinematic which makes the distributor chute rotate around a specified axis.
The steps to set up a kinematic like the one used in this example are outlined in our EDEM tutorials:
Step 6 – Post-Processing
There will be a link to a video showcasing the possible analysis and results that you could obtain from simulating this process in the coming weeks.
Altair EDEM allows engineers in the steel making industry to analyze the charging process in order to:
- Maximize energy efficiency and steel quality by predicting segregation and other detrimental phenomena in the process
- Optimize the burden distribution
- Get detailed structural analysis from realistic data by combining EDEM with OptiStruct or SimSolid
- Analyze material flow and behaviour
- Predict maintenance requirements and wear
- Get an insight into the system at real scale
To find out more about how EDEM can help with optimizing and reducing energy consumption in processes in the steelmaking industry check the following webinar:
If you’d like to see what EDEM users are doing in the Steelmaking industry check this presentation by Edouard Izard from ArcelorMittal:
Applications of EDEM Software at ArcelorMittal R&D
[1] Climate change and the production of iron and steel. World Steel Association. Available at: https://worldsteel.org/wp-content/uploads/Climate-policy-paper-2021-1.pdf.
[2] (2023) Emissions Measurement and Data Collection for a Net Zero Steel Industry. International Energy Agency. Available at: https://iea.blob.core.windows.net/assets/8f6568aa-1dd8-4578-bc61-24ceba4a07dd/EmissionsMeasurementandDataCollectionforaNetZeroSteelIndustry.pdf