Normal Stress in Solid and Shell Model
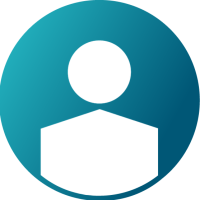

I have created a double sided fillet weld geometry with three plates. This was modeled using solid and shell plate techniques. The case belongs to a normal tensile loading (along X direction as per global coordinate system). Hence, it should ideally possess sigma XX in both the cases. But stress (sigma XX) in shell model is almost 0.25 times the stress obtained in solid model. The stress has been determined at a point farther away from weld, so weld modeling would not be affecting the value in the two cases. This ratio has been consistent even at different load values. I have also iterated the element size varying from 0.5 mm to 3 mm but the deviation has been consistent. So, mesh refinement might not be the reason for this. Please anyone enlighten me with the possible causes.
Thanking you in anticipation.
P.S : I have attached the simulation file (.fem files) for both the cases.
Regards
Venkatesh
Find more posts tagged with
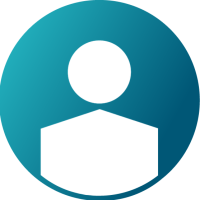

Hey Rahul !
Thanks for your efforts. The stress values which you mentioned above refer to the maximum stress generating in the system. Since the point of stress concentration is different in both cases, comparing these values does not infer anything. If you would look at stress values at similar nodes/elements (for example, at the center node at the loading surface on the center plate ), you would find that stress in shell model is almost one-fourth of that obtained from solid model. Can there be any particular reason for it, and if not could you forward this for clarification ?
Regards
Venkatesh
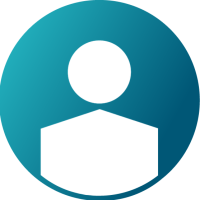

Hi Venkatesh,
As @tinh said the directional stress is not same for both shell and solid.
Please check this.
I think results are intended .We will not get same stress results for shell and solid modelling approach. After run for solid model I see Stress XX as 12.6mpa and for shell as 13.4mpa.
I am moving this query to OptiStruct section for further modelling and analysis clarification.