Free-size optimization un/feasible
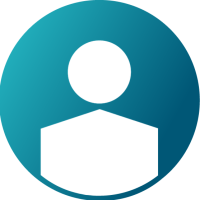

Hello,
I tried to variate the input parameters of my current free-size optimization project. I used starting thickness values of the properties which have proven to be successful before, this is delivering a feasible result with a mass of 400 kg. The optimization goal is to minimize the mass with a constrained buckling factor above 1 and a stress parameter.
Let's say my input thicknesses are not the ideal solution. For this purpose, I tried very large thickness parameters as input, so that the solver can vary them. Instead of 20 mm, I used 100 mm for instance. This is then leading to an unfeasible result, which is (not much but still) violating the buckling constraints. A mass of 200 kg can be achieved.
Can anyone please help me to understand what went south here? I gave the solver more material and more freedom to variate the design variables (=elements), but it couldn't deliver a feasible result. The problem was less constrained than the initial problem. So I expected a better result.
Thank you!
Answers
-
Any ideas how I can solve this problem?
Here is the out-file, if it helps:
It looks like the free-size optimization does not 'see' the buckling constrain at all, the results are getting worse after iterations
0 -