Free Size optimisation Torsion Formula Student Monocoque
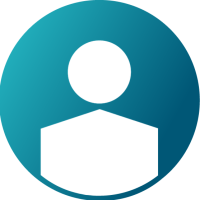

Hi there,
I was trying to do a torsional stiffness optimization model on a formula student monocoque.
I followed the example but there are some details it didn't cover which I was hoping someone on here could help me with.
Firstly is there a way to optimize some plies in a laminate and not others? For example I have some plies which are the base plies in the laminate for the monocoque which I don't want optimized and some 'super plies' which I do. Is there a way to do this?
Secondly I tried a free size optimization, however I have a stiffness target I wanted instead of maximising the stiffness. I set this target through setting a static displacement limit on the two front axle nodes vertically to represent the torsional stiffness. The objective I set was to minimise the total mass, the optimsiation runs, however the thickness results of the elements do not seem to interact across the elements that aren't in the same components. This doesnt seem to be consistant with what is shown in the tutorial but it could be okay, im not sure.
Any help would be appreciated.
Answers
-
Could you share .fem file with us?
0 -
Hi Rahul, I've actually now passed this stage.
Im having a little bit of trouble with the discrete size stage.
At this stage, is it supposed to make all the optimised plies a TMANUF size within the bounds but not get rid of any?
I do a continuous size, targeting minimising mass and the model gets to about 19kg. Which is great.
When I do a discrete, it makes all the plies thicker given the TMANUF constraint however it doesnt get rid of any or make any 0.
Because of this the model rockets up to 40kg which is know is not reasonable.
Does the discrete size optimisation take plies out?
Or does that happen in the shuffle stage, based on the loadcases.
Thanks
0