Hi all,
In my dropping simulation, the energy suddenly rose and the time step was controlled by foam self contact and drop dramatically. From the animation of the process, the mesh of the foam deform dramatically at time t=4.16s, and at the same time the kinetic energy sudden rose.
The engine out file was attached and the contact parameters were listed in file ContactParameter.txt. The contact between the metal plate and the foam was defined and the self contact of foam was also in consideration.
In addition, the part 6 was metal and Ishell=24 QEPH formulation was used. part 86 was foam and Isolid=24 HEPH formulation was used.
So how should I do to solve this problem?
Best Wishes
Roy
<?xml version="1.0" encoding="UTF-8"?>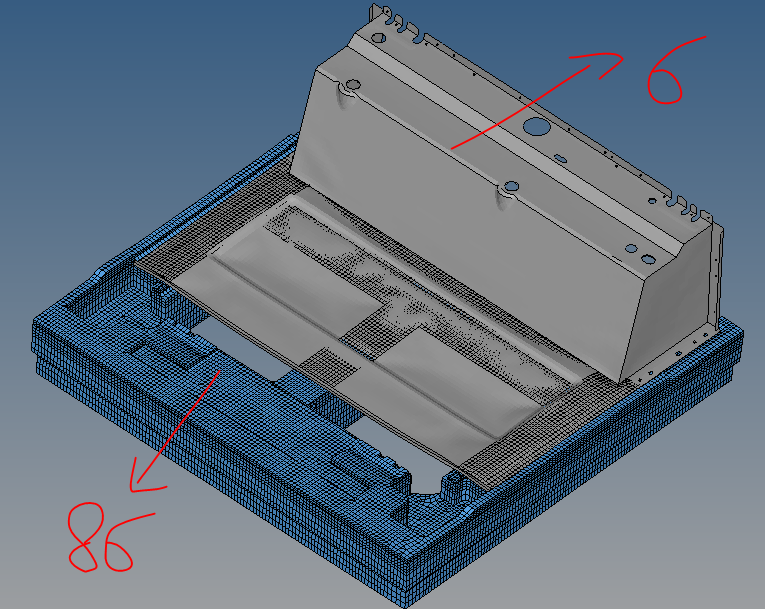
<?xml version="1.0" encoding="UTF-8"?>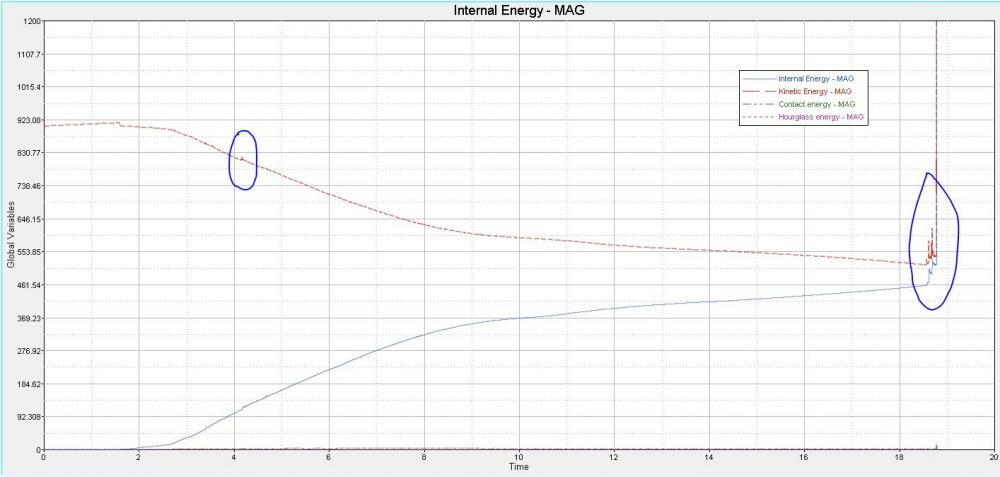
<?xml version="1.0" encoding="UTF-8"?>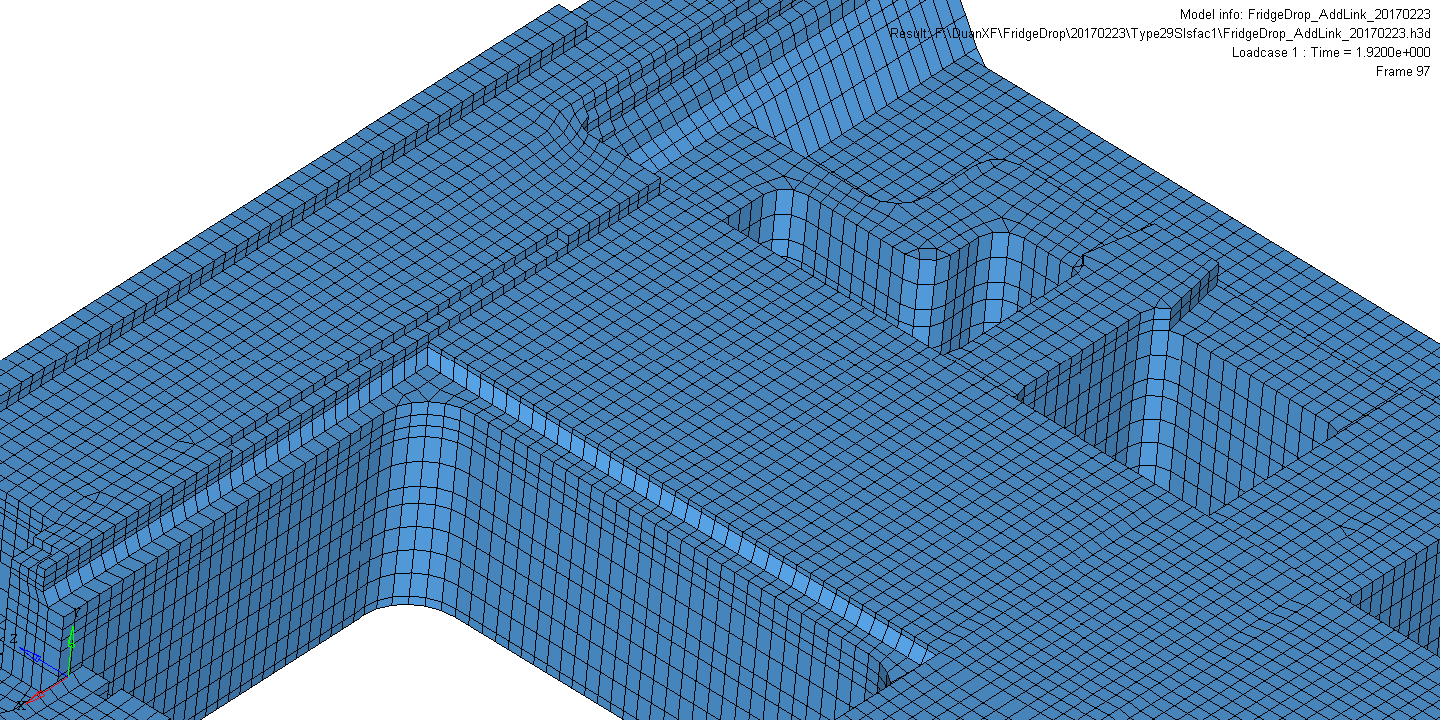
Unable to find an attachment - read this blog