Multiple Loadcases, no feasible design
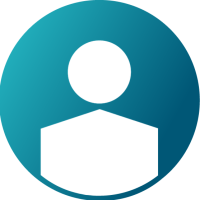

Hy there,
i'm setting up a composite optimization in Hyperworks (Solver: Optistruct) and want to use the displacement of a few nodes (measuring Points) as responses. Every node has its own coordinate system, in which i want to measure the displacement (for example in x-direction). This is caused by the real displacement and measuring directions of the manufactured (existing) part.
The displacements of this nodes should be in a specific range (constraint) in the optimization. This ist how i want to define the stiffness of my model.
I created the systems (by global coordinates, vectors and nodes) and assigned them to the measuring points ( mesh -> assign -> node analysis system).
Afterwards i created the corresponding responses of the same nodes (analysis -> optimization -> responses -> static displacement) and gave them their constraints.
I have three loadcases, whose forces are pointing in different directions.
Mass should be minimized.
Freesize is finished and i have already edited the plyshapes.
After the freesize-optimization I want to get the thickness-distribution of the plies using the discrete-sizing-optimization. The optimization is starting and it also finishes, but it doesn't find a feasible design. According to the solver-output the optimization has converged after 23 Iterations.
What can i do to make optistruct find a global or at least local optimum for my problem?
Is it possible that the objective function 'minimize mass' causes that problem? The existing part has a mass of about 460g, the considered designs in the optimization have about 300g, which seems way to light to fullfill all my constraints.
Thanks in advance,
Andreas Kießkalt
P.S.: I attached the .out file
Answers
-
Hi,
There are few displacement violations on nodes. You need to take care of them. this is written in .out file.
You may have to relax the bounds or increase the thickness of the plies a little and try again.
Instead try to increase the laminate thickness upper bound a little bit and try if this helps.
0 -
Hy,
thanks for your help!
I'll try and let you know if it helped.
Andreas Kießkalt
0 -
Hey there,
i took away the lower bounds of my displacements and now i get a feasible design. But the displacements (according to the postprocessor) are a lot smaller (nearly half of the value) than the upper bounds. Which means that the design could be lighter.
Is there a was to export all displacement values in the .out file so that i dont have to use the postprocessor and select each measuringpoint and ist coordinate System? By now the .out file does not Show all displacement values for all iterations.
Thanks an advance,
Andreas Kießkalt
0 -
Hi,
You can request displacement values to .disp file using Control cards>>Global output request>> DIsplacement>>OPTI.
Let us know if this is not what you are looking for.
0