Loading Force
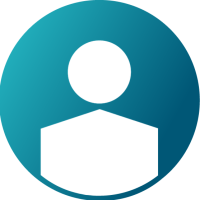

I have a problem with loading forces to my model. when i run the analysis, the component that i load the forces disappear.
here are the screenshot.
<?xml version="1.0" encoding="UTF-8"?>
Find more posts tagged with
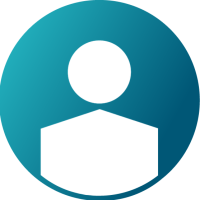

the joint between every component is only contact, no bolt or weld. i drew it in catia, and use contact constraint to assembly.
i know that displacement, it make me confuse.
but then i tried to load the force in another place. and it worked.
why it didn't work when i load the force in that surface before?
here is the screenshot.
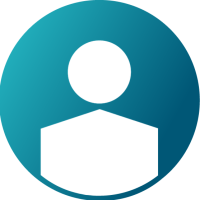
Hi,
It seems a connection problem between the four vertical members and the horizontal plate in the centre. First run, no connection causes rigid motion of the plate and thus high displacements. Second run with load applied on the vertical member which is fixed from bottom and thus cannot undergo rigid motion and hence less values of displacement.Also zero displacement everywhere else as there might not be any connection between these multiple bodies.
For identifying this issue, run a normal mode analysis in optistruct and if you get only 6 rigid body modes and the 7th has a definite frequency the connection is ok , but if you get more than 6 rigid body modes check the animation of modal analysis to find the connection issues.
Please check the interface between your loading component and the structure. I think you have forgot some assembly links between them?
Have a look at displacement value of your results. 4.966E+12, really?