best way to model composite with insert and core and giving force from mounted product
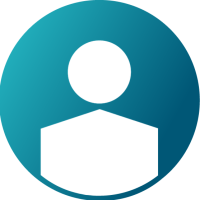
Greetings, and thanks a lot for your help. I learn a lot from this community.
What I’m trying to do is modeling a drivetrain mount and the composite monocoque body and figuring out how drivetrain mount affects monocoque. The situation I want to simulate is when the car starting to move from stop how forces will go through mount to monocoque. And I’ve encountered some technical problems.
- I’ve done some analysis using NLEXPL and this would be a good choice of solver for this kind of analysis?
- The composite laminate should have 2 zones basically, with aluminum honeycomb or with gfrp insert and both of the skins are cfrp. This is how I tried modeling it. After the post processing, the gfrp part seems like falling apart from the laminate and I guess my way is not right. Any possible improvement for this?
- Using rbe element on the shell nodes on laminates does it affects to whole laminate thickness?
Thank you for your time.
.hm and .mvw files below for better explain
Answers
-
1) using explicit depends on what you're trying to analyse. Usually it is used for dynamic problems with a wide group of non-linearities, such as complicated contact conditions. Usually we run a very small time frame, as the timestep is usually small. So usually a few miliseconds of time. In you case, everything looks to be in static equilibrium, and everything is connect, then, probably implicit analysis would do the job.
2) it is hard to tell only by looking your pictures, but I would check better how your material properties are defined, and double check if the units are consistent. Are you plotting displacements with scaling factor? or is your animation showing 1:1 scale?
Looks like your material properties would need a verification, to make sure everything is ok.
Have you tested first, changing the botton and top plates for an aluminum plate, and run your model? If running with this, the model looks fine, maybe there's something wrong with your composite properties.
3) RBE2 always affects the stiffness of the underlying shell, as it introduces mathematical stiffness to the connected nodes. But this should result in "infinite" local stiffness, with no relative movement. It should not give you lower stiffness.
0