Thermal time step, stability limit and correct meshing in Radioss thermal transient simulation
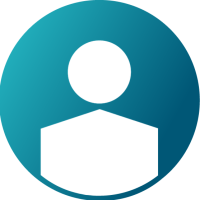

Hello,
I have been trying to understand and adapt the Radioss Thermal Example (RD-5300), in order to make it represent the stress relief procedure. Alternatively, as the time of operation is relatively short, one might think of it as a welding process, with a lot of heat input into the material and generating large temperature gradients.
I have been using HW2017.2.
The assumptions are as follows:
1. The 'weld' along a square trajectory is subject to a high thermal load from the 'Source'.
2. The 'Source' has a constant temperature of 1300 K, and transfers heat through Inter/Type7 to the plate. The coefficient of exchange is high (1000 units), in order to provide a lot of heat in limited time.
3. The heat transfer is based on the actual temperatures of both components (i.e. Ithe=1).
4. The convection heat transfer coefficient is arbitrarily chosen as 1.0, and the ambient temperature is set to 298 K.
5. The initial temperature of the plate is 298 K, i.e. it is the room temperature.
Now, the results are puzzling. I particular, I obtain some negative temperatures on the contour plot, and there are temperature 'waves'/'oscillations' on the model.
I suppose it is associated with the thermal stability conditions and the mesh sizing, but
- RADIOSS does not generate any warning
- I guess the Help system has some gaps in the relevant topic, and I am not able to figure out how to correct the model. In particular, /DT/THERM, according to the Help page seems to require no parameters, whereas I suppose it should work like /DT or /DT/NODA. I find as well the /THERMAL topic very limited, and I do not know how to properly use the time scaling for thermal material data
- In particular, I do not now to interpret the time stability limit. Should the time chosen be smaller than the one calculated from the formula, or rather larger?
- In the help system, I could not find hints on correct meshing for a thermal transient problem
- I was not able to find a means of making Radioss (or HyperMesh, or HyperView) estimate and present the local values of thermal stable time step, and the time step chosen for the simulation seems to be derivced from the standard 'mechanical' Courant condition. Artificial reduction by /DTIX did not help in this case.
Please shed some light on the topic
Regards and thanks in advance
Marek Augustyniak
Poland
Answers
-
Altair Forum User said:
Now, the results are puzzling. I particular, I obtain some negative temperatures on the contour plot, and there are temperature 'waves'/'oscillations' on the model.
I suppose it is associated with the thermal stability conditions and the mesh sizing, but
- RADIOSS does not generate any warningI don't see any negative nodal temperatures in the results. Can you share an image, please?
Altair Forum User said:I guess the Help system has some gaps in the relevant topic, and I am not able to figure out how to correct the model. In particular, /DT/THERM, according to the Help page seems to require no parameters, whereas I suppose it should work like /DT or /DT/NODA. I find as well the /THERMAL topic very limited, and I do not know how to properly use the time scaling for thermal material data
If the time step is too large analysis will not proceed. I think for thermal analysis you can use /DT/NODA/
0 -
FYI,
The explicit time discretization method requires a time step smaller than a critical value tcr.
0