Forming Discussion
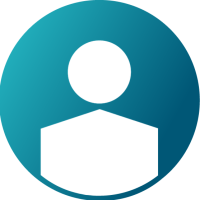
Hello everyone,
I have some questions related to forming simulation which need your consultation.
1. The 1st question is about the “offset value” when creating the tools.
a. By default, the offset factor when creating the tool is 1.2 (gap =1.2*blank thickness)
This value is also applied for the die closing gap.
It’s OK when we have only 1 part of the die set.
Take an example for a single action draw, we have the top die face >> use offset tool to create the punch and binder face >> run simulation.
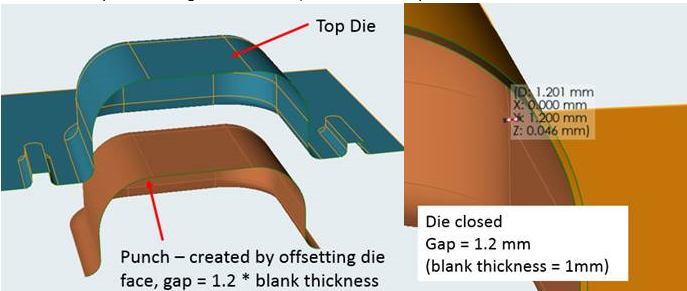
b. However, sometimes, we are provided with a full set of die tools, including the top die, punch, and binder.
And in the design, the gap is only equal to the blank thickness, for example = 1mm.
So what should we do in this case?
i. Take their design faces to use as tools, with the gap between die and punch = 1mm
ii. Recreate the punch by offsetting the die face >> gap = 1.2 mm (as above)
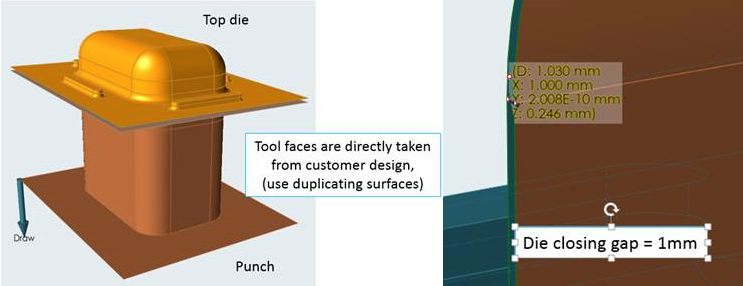
c. I have run a comparison for 2 cases above, the results are slightly different b/w 2 cases.
Other parameters are set the same (mesh size, binder force, friction…)
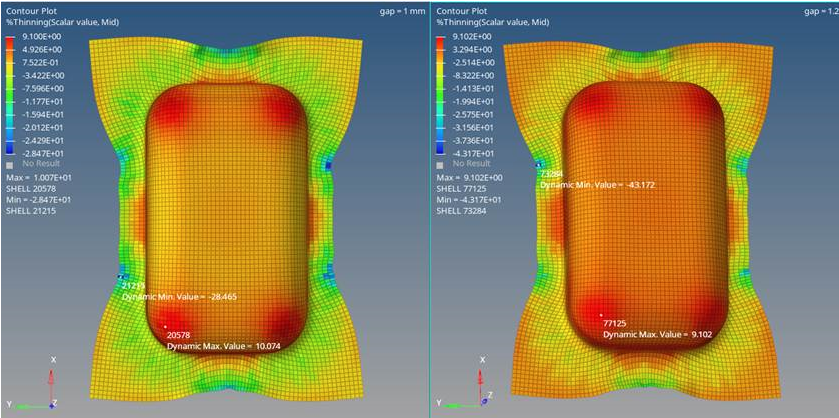
2. The 2nd question is about the material density in HyperForm and InspireForm.
Take an example for steel, rho = 7.8e-9 (ton/mm3)
If I use the uniform mesh size (turn off adaptive mesh), the density is remained originally = 7.8e-9 t/mm3
However, when using both InspireForm or HyperForm with the “adaptive mesh = on”,
The rho is increase 10 times >> new rho = 7.8e-8 (t/mm3) – check the model browser in HF
So may I ask about the purpose of this? Is it used to increase the time step >> reduce solution time?
And does it affect the result?
Since I have also made a comparison b/w 2 cases:
a. Uniform mesh size = 4mm (rho = 7.8 e-9)
b. Min adaptive mesh size = 4mm (rho = 7.8e-8)
The result are also slightly different.
Thank in advance!
Answers
-
The 1st question is about the “offset value” when creating the tools.
a. By default, the offset factor when creating the tool is 1.2 (gap =1.2*blank thickness)
a. 20% offset pattern (total gap will become 1+0.2),
for example, your blank thickness is 1 mm and tool offset is 20% total gap will be blank thickness+20% of blank thickness =t(1+0.2)
b. However, sometimes, we are provided with a full set of die tools, including the top die, punch, and binder.
And in the design, the gap is only equal to the blank thickness, for example = 1mm.
So what should we do in this case?i. Take their design faces to use as tools, with the gap between die and punch = 1mm
you need a little gap here
ii. Recreate the punch by offsetting the die face >> gap = 1.2 mm (as above)
this can be done easily using the offset tool.
2. The 2nd question is about the material density in HyperForm and InspireForm.
Take an example for steel, rho = 7.8e-9 (ton/mm3)
If I use the uniform mesh size (turn off adaptive mesh), the density is remained originally = 7.8e-9 t/mm3
However, when using both InspireForm or HyperForm with the “adaptive mesh = on”,
The rho is increase 10 times >> new rho = 7.8e-8 (t/mm3)2. Check over the unit consistency and compare the model
Regards,
Sourav
0 -
Altair Forum User said:
The 1st question is about the “offset value” when creating the tools.
a. By default, the offset factor when creating the tool is 1.2 (gap =1.2*blank thickness)
a. 20% offset pattern (total gap will become 1+0.2),
for example, your blank thickness is 1 mm and tool offset is 20% total gap will be blank thickness+20% of blank thickness =t(1+0.2)
b. However, sometimes, we are provided with a full set of die tools, including the top die, punch, and binder.
And in the design, the gap is only equal to the blank thickness, for example = 1mm.
So what should we do in this case?i. Take their design faces to use as tools, with the gap between die and punch = 1mm
you need a little gap here
ii. Recreate the punch by offsetting the die face >> gap = 1.2 mm (as above)
this can be done easily using the offset tool.
2. The 2nd question is about the material density in HyperForm and InspireForm.
Take an example for steel, rho = 7.8e-9 (ton/mm3)
If I use the uniform mesh size (turn off adaptive mesh), the density is remained originally = 7.8e-9 t/mm3
However, when using both InspireForm or HyperForm with the “adaptive mesh = on”,
The rho is increase 10 times >> new rho = 7.8e-8 (t/mm3)2. Check over the unit consistency and compare the model
Regards,
Sourav
hi Sourav,
Thanks for your answers.For the 1st questions, in conclusion, we still need to use our offset tool to recreate the die/punch/binder with the gap factor = 1.2 >> OK
For the 2nd questions, i used the same model for 2 tests.
The density automatically increased when turned on the adaptive mesh, no other modifications at all.
You can try yourself with the attached file.0 -
i believe this is being performed as a massa scaling to get a larger timestep (as the mesh will be reduced, density is increased to compasate for timestep reduction).
Probably the problem is not so fast, and increasing a little bit the density allows a increase of timestep with no big losses on acuracy.
0 -
can anybody please tell me that at which direction the bottom binder force is applied, same as drawing direction or in reverse?
and what is actual and correct bottom binder force direction while stamping?
0 -
Hardik Karpe said:
can anybody please tell me that at which direction the bottom binder force is applied, same as drawing direction or in reverse?
and what is actual and correct bottom binder force direction while stamping?
Hi Hardik,
The bottom binder is being used in cases of Single action draw and is positioned below the blank component and the force direction will be opposite to the draw direction as it will be used to hold the blank in its position and clamp it against the top die. And when the forming starts it exerts the resisting force to clamp the blank and moves down with the top die to form the blank.
Thanks.0