Difference in mass, size optimization
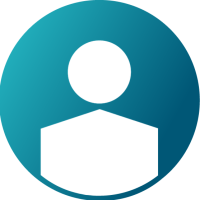

Dear optistruct users,
I have a question regarding the sizing optimization. Currently I am performing a size optimization of a truss structure. The model consists of lines which are meshed into Cbeam elements and design variables are generated in order to perform a size optimization. The design is subjected to multiple load cases. The objective of the optimization is to minimize the mass of the structure. Constraints are defined for the member stresses and displacements. The optimization works fine.
When I calculate the mass of the structure by using tools --> mass calculation, I obtain a mass of 2.056 ton with a volume of 2.620 * 10^8 mm^3. I have used the standard steel material properties (Rho=7.85 * 10^-9 mm^3). I have defined point masses which are defined in a separate compnent with a total mass of 1.245 ton.
When I look at the first iteration step (iteration 0) in the output file. I see that the mass is equal to 2.358 Ton and that the volume is equal to 1.42394*10^8 mm^3. This confuses me.
So to make it clear:
Before first iteration step: Mass= 2.056 Ton
Output file, Iteration zero: Mass = 2.358 - 1.245 = 1.13 ton
I understand that the masses of the point masses are incorporated into this mass. But why is the volume changed of the design?
On the internet I found the following written about this difference, but it is still not clear for me.
Do I make a mistake, how should I interpret these masses?
Can someone make this clear for me?
Regards,
Michael
The problem is solved. The difference is due to the fact that in hyperworks the volume of the beams is defined by the beam dimensions from hyperbeam. While in Optistruct, the optimizer uses the initial values specified in the design variables. This explains the difference in volume and therefore also in mass. I was confused by that but now I hope this is also clear for other users.
Regards,
Michael