Mass addition in master element of Type 2 contact
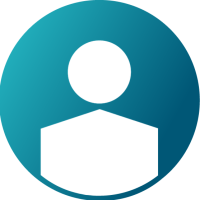

Hello everyone,
Greetings!!
I have made seam weld elements between 2 components. Then I made tied contact (Type 2 contact) between these components by considering seam elements as master component.
But when I ran the crash simulation mass of 720 kg was added in these seam elements, which made the entire mass of my crash sled 3.5 times heavier than the actual weight.
I have to use tied 2 contact as I wanted to use the contact interface for spot welds.
I cant omit DT/NODA/CST, otherwise my simulation time is increasing exponentially.
Because of crash simulation, some elements are deforming to a very small length.
Thanks in advance.
Regards
Nitin Jain
Answers
-
Hi Nitin jain
When you create a spot weld using type 2 spring in seam, by default you will get the (TYPE13 spring property + TYPE2 contact).Please do change the values of parameters as per your model unit system.
0 -
type 2 tied contact interfaces with spotflag=1 will add mass. From Radioss help:
0 -
Thanks @Pooja S
I am using Hexa (tapered T) type seam weld and I gave desired properties to it.
Thanks @Ivan
I ran the simulation again with switching off Spotflag. It solved my problem.
But is my contact now simulating the exact condition of spot weld or not.
Because from Altair manuals, I learned that Spotflag=1 represents the condition for spot welds, etc.
How accurate are the results with Spotflag= off.
Thanks and Regards
Nitin Jain
0 -
The slave nodes height with respect to the master segments should be as small as possible. Indeed, the geometrical concordance is necessary for Interface Type 2 to work normally, and will help to get a lower added mass. Please go through the FAQ in Help Menu on Kinematic Conditions where this is well explained.
Using fully integrated elements in combination with spotflag=0 is OK, but rotational DOFs are not transmitted.
Check the attached documents for details.
0