Design non- design section problem
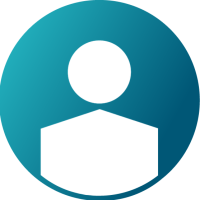

I have applied forces on the face of gear and contraints at the centre, to run optimization I have created design part and and non-design part and then I meshed them together applied forces and constarints on the non- design part but when I ran the analysis there is no stress distribution in design part
I think the error is because my to mesh are not connected
How to solve this error
<?xml version="1.0" encoding="UTF-8"?>
Find more posts tagged with
- if nodes at the interface between design and non-design space are reasonably close together (matching) you can use tool>edges panel (shift+F3) and equivalence the nodes.
- If the nodes at the interface are not matching you can use tie contact to connect the components.
- If the above approaches fail, then you should remesh the components, making sure the mesh on the surface at the interface is used as a seed (Fixed trias/quads to tetra mesh) when tetrameshing both components.
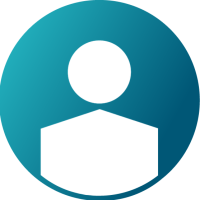
Hi,
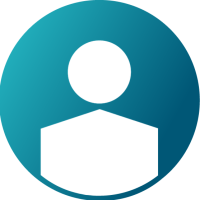
TIE contact can be automatically created using tools>contact browser>AutoContact
https://altairhyperworks.com/pdfs/tips/1095.pdf
Tie contact can also be created manually by analysis>interfaces>create as type=TIE
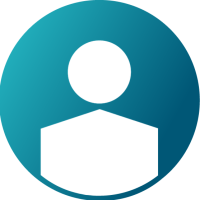

TIE contact can be automatically created using tools>contact browser>AutoContact
https://altairhyperworks.com/pdfs/tips/1095.pdf
Tie contact can also be created manually by analysis>interfaces>create as type=TIE
Thank you.
I created the tie contact and the analysis was successful I got the stress distribution in both design and non-design components. But the problem is maximum stress value before splitting the whole component into design and non-design design part was less than the results that I got. According to me the stress values should be same before and after splitting component into design and non design space.
Please comment on this..
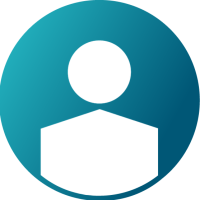
Glad to help.
Actually, the stress should be slightly higher in the localized area around the tied interface because of different load transfer mechanism (as moment loads due to misalignment between nodes, but I'm not sure).
The difference between the effects of two different but statically equivalent loads becomes very small at sufficiently large distances from the load (Saint-Venant’s Principle).
If you aren't specifically interested in localized stress around the interface tie can be used, otherwise proper node to node connectivity is preferred.
1st photo is total load case with constarints
2nd pic is design part
3rd is non-design