Robotic Hand Prosthetic Motion Analysis in Altair Inspire
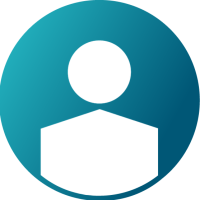

INTRODUCTION
The human hand is incredibly versatile, being able to pick up a large range of objects of different sizes and shapes while supporting large weights. It is natural that robotic engineers look to the hand for inspiration in the design of new robotic systems. In fact, many groups have developed iterations of humanoid robot hands. Humanoid robots are making use of human-inspired hands to pick up boxes, use tools, and pour drinks. NASA and GM saw success with their Robonaut 2, the first humanoid robot in space, which made use of cutting-edge robotic hands to perform simple tasks alongside astronauts. In a partnership with Bioservo Technologies, NASA and GM developed a robotic grip-strengthening glove to aid factory workers. Robotic hands also have applications in prosthetics where functional robotic hands can be used in place of cosmetic prosthetics to improve life for amputees.
In the development of robotic systems like the robotic hand, the mechanisms require complex linkages to mimic the motion of the human hand. The motion of such linkages is difficult to visualize, and prototypes can be time-consuming and expensive. Multibody dynamics (MBD) simulation allows for the visualization of such mechanisms. Precise control afforded by MBD lets users simulate the motion of any desirable behavior possible with the robotic hand. In addition to mechanism kinematics, MBD can predict the forces throughout the hand. Forces can provide insights into the load paths throughout the hand and act as boundary conditions for FEA to determine whether the hand will break. The torques at motors can be used to size motors properly to ensure lightweight, but powerful design.
Building a Robot Hand MBD ModelIn this example, we will set up an MBD model of a robotic hand and demonstrate a few applications of the model. The model is built using Altair Inspire, an intuitive tool with features for semi-automated model building all while leveraging accurate, industry standard solvers. The general modeling steps include:
- Importing geometry into Inspire
- Grounding the wrist component
- Creating rigid groups for components fastened together
- Building joints
- Building couplers to represent all gear pairs and ACME screw connections
- Creating contacts for all pins in slots
- Creating torsion springs with preload to maintain the finger’s curled position
- Building motors to drive each finger and the thumb
- Creating custom motion profiles for each motor to generate the desired motion
Inspire (2024 or newer)
MODEL FILES RUNNING THE MODEL- Choose & open one of the .stmod files found in the zip file using Inspire
- Use Analyze Motion in the Motion tab to run an analysis
- View the results
The robotic hand is capable of performing a wide range of gestures including the thumbs up and a finger flutter.
Thumbs Up Gesture with a Robotic Hand
Thumbs Up Gesture with Hand Cover Removed
Finger Flutter Motion with a Robotic Hand
Finger Flutter Motion with Hand Cover Removed
Multibody dynamics also allows users to create simulations of a robotic hand picking up objects. The force explorer can be used to show the contact forces between the object and each finger. The force explorer can also show the forces in joints which indicate the load paths through the hand. The forces on the joints can be used to inform FEA to determine the stresses in individual parts. Additionally, the torques required by each motor can also be extracted and plotted. This technique can be used to develop specifications for motors and actuators.
Water Bottle Grab
Water Bottle Grab Joint Forces in the Force Explorer
Pointer Finger Stresses Holding the Water Bottle
CONCLUSIONRobotic hands represent important developments in the field of robotics. Despite improvements, more work needs to be done to match the power and versality of the human hand. Simulation is one avenue for designing new mechanisms and validating the performance of new materials. Multibody dynamics can assist designers by visualizing the complex mechanisms and predicting load paths through the hand. Loads can be used to generate the requirements for new actuators and motors to meet the desired grip strength and precision of new robotic hands. Additionally, engineers can simulate the pick and place operations on a wide array of objects to validate system performance before manufacturing and testing.
AUTHORSJohn Dagg, Systems Engineering Intern
Christopher Fadanelli, Solution Engineer – Systems Integration
Ananth Kamath Kota, Global Technical Manager – Systems Integration