Light Armored Vehicle Off-Roading and Rough RoadSimulations with MotionSolve,EDEM, and Twin Activate
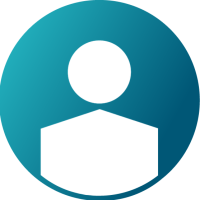

Light armored vehicles (LAVs) are versatile military vehicles with a balance of mobility and armor. LAVs can operate on-road and off-road in harsh environments. Off-road environments can range from hot, dry deserts to rocky mountain environments to cold, icy tundras. The harsh terrains necessitate a powerful drivetrain, robust suspension, and an intelligent control system capable of handling any environment. Achieving the desired performance requires thoroughly validating the system under a range of conditions. Unfortunately, collecting operational data is limited by the available environmental conditions, time, and money. Fortunately, simulation can complement physical testing by providing the ability to analyze vehicle performance in different environments, maneuvers, and loading conditions. Simulation can also allow engineers to test different designs earlier in the design process before changes become more expensive and difficult. In this example, a comprehensive simulation handles the dynamics and controls to provide an analysis which is accurate to the operating conditions of an LAV.
Figure 1: LAV 8x8 Model
Figure 2: Validated Soil Representation with Different Particle Sizes
Understanding the ModelThe Multibody Dynamics Model - MotionSolve
Figure 3: Multibody LAV Model
The multibody dynamics are handled by Altair MotionSolve. A vehicle tools library expedites the vehicle assembly process, allowing for the creation of drivetrain, suspension, and steering systems. Afterwards pre-built components can be populated with design data. An MF-Swift tire model uses an elliptical cam contact method to accurately predict vehicle dynamics which allows for the analysis of vehicle handling and durability. The control arms are replaced with flexible bodies which account for the deformation of the control arms and allow for the calculation of stresses on the control arms. Stresses can be used to identify stress hotspots for fatigue analysis.
The Control System - Twin Activate
Figure 4: Driveline Controls
A controls system built in Twin Activate handles the torque applied to each wheel to provide accurate control while minimizing slip. A controller compares the vehicle’s target velocity and actual velocity to calculate the torque to apply to each wheel. The LAV also implements traction controls to prevent unnecessary slippage while traversing rough terrain. To accomplish this, the controls system monitors the velocity of the vehicle and each wheel. If the wheel velocity significantly exceeds the velocity of the vehicle, the vehicle reduces the torque applied to the wheel to stop the wheel from spinning out.
The controls system is exported as a Functional-Mockup Unit (FMU), a standard which allows easy integration with a range of simulation tools for complex multi-physics analyses. The FMU is integrated with the MotionSolve multibody dynamics model. The FMU receives information about the velocities of the MBD model and outputs the torques to apply at each wheel.
The Bulk Material Model - EDEM
Figure 5: The Bulk Material Model
The bulk material model, built in EDEM, consists of a validated bulk material model representing sand and gravel. A Hertz-Mindlin contact model accurately handles the forces between the particles and the vehicle. The coupled MBD and discrete element method (DEM) allows for the simulation of a range of different bulk materials like sand, dirt, gravel. For this simulation, the sand and gravel are built into a series of hills which the LAV can traverse.
Software RequirementsMotionView - 2024 or newer
MotionSolve - 2024 or newer
Twin Activate - 2024 or newer
EDEM - 2024 or newer
Model FilesLAV_Models.zip (Download Model Files)
Running the ModelReplacing the control arms with flexible bodies allows the solver to compute stresses and deflection of the control arms at every timestep. Contour plots, like one shown in Figure 9, can be used to identify stress hotspots. Stresses at critical locations can be used to inform fatigue analysis to determine the life of the component.
Figure 14: Lower Control Arm Stress Hotspots
LAV Results: Rough Road Traversal
A second version of the LAV model was constructed to evaluate the vehicle’s performance through a rough road course. The course consists of a slalom course, bumps, ditches, and steps. The simulation can be used to evaluate the handling and performance of the steering and suspension systems. Throughout the course, a control algorithm maintains a target with the LAV’s weapon. The control algorithm can be refined and tested to optimize performance.
Figure 15: LAV Rough Road Course
Figure 16: LAV Slalom Course
Figure 17: LAV Rough Road Traversal
ConclusionSimulation is a powerful tool which can supplement physical testing in areas where testing isn’t realistic due to lack of available conditions and costs. These benefits are particularly important in the development of vehicles like LAVs where they need to be designed to handle a wide range of conditions. Co-simulation that handles the multibody dynamics, controls, and soil interactions can provide valuable insights into vehicle performance under countless scenarios. A model can predict the tire slippage or required torques to perform a maneuver. A new control system can be tested and refined to maximize performance. Alternatively, critical components can be replaced with flexible bodies, providing insights into the stresses required for fatigue analysis. Together with physical testing, simulation can provide crucial insights into system performance, saving time, money and leading to better designs.
AuthorsJohn Dagg, Systems Engineering Intern
Christopher Fadanelli, Solution Engineer – Systems Integration
Ananth Kamath Kota, Global Technical Manager – Systems Integration