Regarding Composite optimization in optistruct
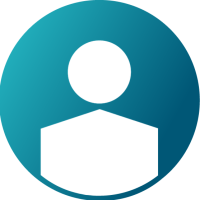
Answers
-
Hi,
By "didn't get the solution", do you mean the optimization cannot find a feasible design?
Here is my suggestion:
1. Please check the .out file and see what constraint is violated.
2. Before you do free size optimization, you just need to create one ply with each orientation with maximum possible thickness. I remember free size will only reduce the thickness but will not increase over the initial ply thickness.
3. Free size is more like concept design, it is better not to put all constraints into the problem at this stage. You may minimize mass while constrain the displacement. You may add a few manufacturing constraints such as balance and max thickness percentage of each angle.
4. You may need to run multiple free size optimization with slightly different setup to give you better insight. The purpose of free size optimization is not to provide a feasible design directly, but to give engineers some insight of the problem's nature.
5. Based on the results from multiple free size runs, create the ply shapes of each ply. Make sure the ply shape is reasonable and manufacturable. Assign a proper thickness upper and lower bound for each ply.
6. When you run sizing optimization after step 5, you may include more constraints such as composite failure.
0