Car Frame optimization
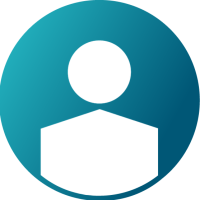
I am optimizing the car frame by considering the entire design mass available with the help of Optistruct (you can imagine it as a hollow solid car body, separated into three compartments (first for engine, second for driver and seats and third for some payload). The parameters I set for the optimization are as follows:
Boundary Conditions: Fixed support at fours wheel connections
Forces: Bending, Torsional, lateral (braking) and gravitational forces
Design variable: Element Density
Design constraint: Static displacement for multiple load cases with an upper bound of 60mm.
Objective: Minimum Mass
Optimization Controls: Minimum Member size = 60mm, Discrete = 2, MATINIT = 0.6 and MINDENS = 0.00001
With these optimization formulation and controls, I am getting load paths of the car frame in the vertical directions but not in the horizontal direction.
Could anyone please explain me what am I missing in the formulation? or Is there any other methods/ controls through which I can improve my optimization to find proper loadpaths?
Answers
-
-
Thanks for your reply @Rahul R. I will try these formulations to see if I can get a better result.
and yes, I have applied manufacturing constraints (min. member size = 100mm; max. member size = 200mm; min. gap = 200mm + Extrusion). I would like to add symmetry through pattern grouping, but unfortunately extrusion+pattern grouping is not supported. Could you possibly know any other combination(s) of manufacturing constraints for better results.?
0