Rubber shell in Radioss
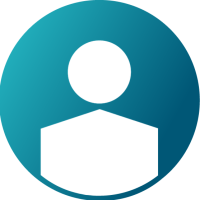
Hello, I am trying to model the correct bending stiffness and rebound and damping behavior of a rubber plate. My plate is meshed with 3mm shells adn 6mm P1 property. I tried with Mat Law2 and Law69 and in both cases my model 'explodes' on the rebound. See images below and both model files attached. Any help in figuring out what I'm doing wrong?
Thanks!
<?xml version="1.0" encoding="UTF-8"?>
<?xml version="1.0" encoding="UTF-8"?>
<?xml version="1.0" encoding="UTF-8"?>
Answers
-
Hi,
when the shell element size is small compared to thickness it loses validity.
<?xml version="1.0" encoding="UTF-8"?>
When h/L is large, shear deformation is at its maximum importance and the user should use solid elements. When h/L is small, transverse shear deformation is not important and thin shell elements are the most effective choice.
https://www.linkedin.com/pulse/shells-vs-solids-finite-element-analysis-quick-review-kuusisto-p-e-
Solid elements are more appropriate and the simulations runs fine.
0 -
Thanks for your input Hyperman. I was hoping to be able to pull it off with shells but was expecting the large h/L ratio of my elements to be a problem.
Spin off question for rubber in Radioss; how can I introduce damping in the material? As it is 100% elastic with Law2, it just 'flaps' around indefinitely, which my real part does not do!
Can damping be introduced 'directly' in the material properties with another material law? Or must it be externel (ex. Rayleigh, DYREL, etc.)? If external, which is best to use?
Keep in mind that I will have many rubber plates like this one moving at relatively high speed (100+km/h) impacting stationnary objects. I don't want the external damping to affect the overall correctness of the simulation but I need to properly represent the 'internal' damping of the rubber.
I would have access to a physical test to calibrate the damping of my model.
Thanks
0 -
Glad to help.
Damping can not be defined in the material properties (like in Optistruct). Rayleigh damping /DAMP and dynamic relaxation /DYREL/1 can be applied to a group of nodes to avoid damping the whole model. Use the damping type that achieves primarily a better correlation to the experiments and secondarily better computational efficiency.
0 -
Greatly appreciated, Thanks Hyperman!
0 -
The issue with LAW2 is that it is linear elastic. For Non-linear elasticity, you can use one of the hyper-elastic materials like LAW42, LAW69, LAW92, or LAW94. Example 'RD-E: 5600 Hyperelastic Material with Curve Input' shows more details about these materials.
To viscous (rate) effects to the material you can use the viscous input in LAW42 or add /VISC/PRONY to the other materials. However, data for the viscous input is difficult to determine. So then maybe Hyperman's suggestion of Rayleigh damping /DAMP would be easier.
Thanks,
Andy
0 -
Altair Forum User said:
I am solving plate for modal ansly with
two sides clamped two sides free
And
One sideclamped three sides free
How to apply two constraints in a single model
It says specify bc=n ... Which I don't know
0 -
https://community.altair.com/community?id=community_question&sys_id=745680f61b2bd0908017dc61ec4bcb32
I am solving plate for modal ansly with
two sides clamped two sides free
And
One sideclamped three sides free
How to apply two constraints in a single model
It says specify bc=n ... Which I don't know
0 -
Hi @Sony Dhotre
create a separate load collector for each set of boundary conditions. For example, create a load collector with all DegreesOfFreeedom fixed and a second load collector fixing only translational DOFs. Create only one load collector if you need to constrain only one set of DOFs.0 -
Altair Forum User said:
Hi @Sony Dhotre
create a separate load collector for each set of boundary conditions. For example, create a load collector with all DegreesOfFreeedom fixed and a second load collector fixing only translational DOFs. Create only one load collector if you need to constrain only one set of DOFs.Altair Forum User said:Hi @Sony Dhotre
create a separate load collector for each set of boundary conditions. For example, create a load collector with all DegreesOfFreeedom fixed and a second load collector fixing only translational DOFs. Create only one load collector if you need to constrain only one set of DOFs.0 -
here is the bdf file
i am getting error as
USER FATAL MESSAGE 9073 (SUBDMAP PHASE0)
MULTIPLE BOUNDARY CONDITIONS IN NORMAL MODES ANALYSIS REQUIRES THE BC=N COMMAND IN EACH RESIDUAL STRUCTURE SUBCASE.0 -
-
The solver deck you shared is a Nastran bdf file and that error was reported by a Nastran solver. Nastran issues should be posted on Nastran forums (this is Altair forum).
Optistruct can import bdf files and I was I able to run your model without issues- see attachments.
0 -
sir also i want to apply simply supported boundary conditions for plate on all four sides.
plate will have only rotation not translation on all the edges is it correct, if not correct me.
thanking you
0 -
Attached is the model file and result for a simply supported plate on all four sides.
0 -
thank you sir
0 -
I want execute the model
the bdf file is larger than the limit so i couldn't uploaded.
hope you understand.
it is for the modal analysis.
thank you sir
0 -
I can help you learn, but do not expect me to do your work.
First try yourself and ask for help only if you fail.
0 -
Good Morning Sir,
by accepting your advice, i want to convey to you that.
i am getting some different results than expected.
as I am executing a model referring a paper.
the material for face and core is aluminum.
i am using MAT1 for face and MAT9 for core.
PSHELL PSOLID
i am suppose to get the frequency 20<= f <= 30 in Hz
i am getting 1.36Hz for 25 element size
0.7809 hz for 20 element size
Geometric Details
A =1828.8mm
B =1219.2mm
Tc =6.35mm
Tf =0.4064mm
a/b =1.5
Material Properties
Face Aluminum Aluminum Core
E= 68.94 GPa G23 = 51.71 e-3 GPa
G= 25.92 GPa G13 = 134.45 e-3 GPa
V= 0.33
P= 3.05E-09 tn/mm3 p = 1.34 e-10 tn/mm3
121.8318 kg/m3
Cards Used
MAT 1 MAT9
PSHELL PSOLID
SSS Boundary Condition
correct me if anything is wrong
thank you sir
0 -
There is an issue with the material property matrix (Gij)- it fails the material check:
*** ERROR # 1551 ***
for material id = 1 referenced from property id = 1.
Material coefficients Gij on MAT9 card produce material matrix with negative eigenvalues. This violates material stability conditions.
Eigenvalues of G: -1.440511e+02 1.956294e-15 1.440511e+02
0.000000e+00 0.000000e+00 0.000000e+00If the material check is disabled (PARAM>CHECKMAT>NO) I get the same results.
0 -
Good Evening sir,
i really thank you for the support that i am having from you. it means a lot.
i want to get clarity, is this the problem of material property value input G13 , G23 ......or else.
i don't find any checkmat in hypermesh v9.0 as i am using in conjunction with nastran.
thank you sir
0 -
Glad to help. You can show appreciation by liking the content.
Yes, the issue is with the G13 , G23 parameters. Are you sure you are not confusing the material property matrix parameters (Gij) with the shear modulus? If material data is specified with the Engineering Constants E1, E2, E3, NU12, NU13, NU23, G12, G23, and G13, then use the MAT9OR data.
Analysis>control cards>PARAM>CHECKMAT>NO, but it is possible CHECKMAT is not supported in HM 9.0. It will not solve your problem as mentioned before.
0 -
good evening sir,
i have downloaded hwv19
i am not finding any checkmat
thank you sir
0 -
-
yes sir i got it,
its there in hmv9.0 also.
i tried but its giving different results.
There is an issue with the material property matrix (Gij)- it fails the material check:
https://community.altair.com/community?id=community_question&sys_id=745680f61b2bd0908017dc61ec4bcb32 Quote*** ERROR # 1551 ***
for material id = 1 referenced from property id = 1.
Material coefficients Gij on MAT9 card produce material matrix with negative eigenvalues. This violates material stability conditions.
Eigenvalues of G: -1.440511e+02 1.956294e-15 1.440511e+02
0.000000e+00 0.000000e+00 0.000000e+00If the material check is disabled (PARAM>CHECKMAT>NO) I get the same results.
can you send me the results
0 -
i need to get frequency of 20<= f <= 30 hz
checkmat is there in hmv9.0 also
0 -
As mentioned before, I get the results much lower than required. The probable cause of difference is inappropriate material properties.
0