Negative % ERROR IN RADIOSS
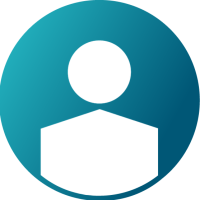
Hello everyone,
i am facing negative % ERROR in radioss, due to % error convergence issue is occurring.
for reference i am attaching the .out file.
pls let me know how can i resolve the issue.
One thing i want add is this % error is occurring when ever i am using contact between master and slave component,
i am sure there is no any penetration between slave and master.if i am simulating the problem without any contact , like directly applying load on component node,
there is no issue occurring.for reference i am also attaching the snap shoot of contact assignment.
<?xml version="1.0" encoding="UTF-8"?>
regards
Answers
-
Hi,
Use the recommended contact parameters for interface Type 7:
Istf=4
Igap=2
Fscale_Gap=0.8
INACTI=6
Gap_min=1
Fric = 0.1
Iform=2Another reason for timestep drop and energy error is because Interface type 7 does not deal with edge to edge impact. When the mesh is fine enough, edge to edge penetration is often followed by a node to shell contact. The main problem with edge to edge impact is the locking situations. If there is a change of load after edge penetration, locking is unavoidable since a node to surface contact is detected. This usually leads to high penetration; therefore, the analysis comes to a standstill as time step is reduced. If locking occurs, the use of interface type 11 in this area is necessary to solve the problem.
Share the model file if the issue persists.
0 -
Altair Forum User said:
Hi,
Use the recommended contact parameters for interface Type 7:
Istf=4
Igap=2
Fscale_Gap=0.8
INACTI=6
Gap_min=1
Fric = 0.1
Iform=2Another reason for timestep drop and energy error is because Interface type 7 does not deal with edge to edge impact. When the mesh is fine enough, edge to edge penetration is often followed by a node to shell contact. The main problem with edge to edge impact is the locking situations. If there is a change of load after edge penetration, locking is unavoidable since a node to surface contact is detected. This usually leads to high penetration; therefore, the analysis comes to a standstill as time step is reduced. If locking occurs, the use of interface type 11 in this area is necessary to solve the problem.
Share the model file if the issue persists.
hi hyperman,
As per your recommendation i have change the contact interface TYPE 7 to interface TYPE 11 but i am facing same kind of issue,
for your reference i am attaching .hm, radioss exported file and .out,
requesting you to pls check l and resolve the issue,
pls send the corrected model.
Regards
Noor Alam
0 -
hi hyperman,
As per your recommendation i have change the contact interface TYPE 7 to interface TYPE 11 but i am facing same kind of issue,
for your reference i am attaching .hm, radioss exported file and .out,
requesting you to pls check l and resolve the issue,
pls send the corrected model.
Regards
Noor Alam
0 -
Hi,
Large contact energies relative to total energy can cause large negative Energy Errors because contact energy is not part of the Energy Error equation. If the simulation has friction and a lot of sliding contact, then the large contact energy and resulting energy error can be considered acceptable.
<?xml version="1.0" encoding="UTF-8"?>
0 -
hi,
if contact energy is going in negative, then what should i do, should run the simulation or cancel.
because your corrected model has also negative energy error. i have little bit doubt is it give correct
result or not.
also please confirm should i used contact interface Type 7 and Type 19 together. which used
by you in corrected model. or anyone contact interface type.
please suggest.
regards
Noor Alam
0 -
Hi,
the negative energy error can be considered acceptable in this case due to sliding contact with friction and the energy is transferred through the contact interface. As the contact energy is increasing at a slower pace than the total energy (plots are diverging) the energy error percentage will reduce throughout the simulation.
Only type 7 contact interface can be used since there is no edge penetration issue.
0 -
THANK YOU VERY MUCH, for your support.
i want to know for highly impact load (Initial velocity) which contact interface type will be preferable,
if loading condition is similar to my model,
Regards
Noor Alam
0