How to electrically control a proportional valve
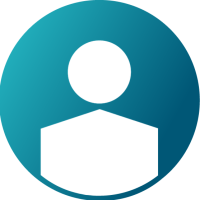
Hello,
I am attempting to model an electromechanical system where potentiometers control the valves, thus limiting the flow to a motor. Short version of that is I am using a potentiometer to control a hydraulic motors' speed. The 90L100 Pump, 90L100 Charge Pump and mostly everything on the bottom of the model works as it should with no issue. The potentiometer superblock also works perfect as I verified with hand calculations. The problem arises when I am attempting to connect the potentiometer to the valve and the motor. The results being observed in the scope are very odd. Placing the rConstant potentiometer anywhere below 0.3 results in a crazy waveform in the negatives and anything above that produces a straight line down to about negative 30 at 30 second run time.
This is very likely to be a complete user error as I am still new to this software so I am looking for some guidance/recommendations on what valve to use and how to hook the potentiometer to it to control its flow. Below I have attached an image of the whole model but as I said above the only problem is with the potentiometer and propvalve.
Any help would be greatly appreciated!
Answers
-
Hi AJ,
That's interesting, can you share your model so I can have a better look and advice?
1 -
Hi AJ,
Are you intentionally using a load-sensing valve? The ls-port (connected to pump and motor) only represents a pressure, the flow is internally not connected to port A or T. This could disturb the entire system.
I'm not sure how you want to control the motor, but typically you could use a standard directional valve (PropValve43PT2) to control speed and direction of the motor.
Unfortunately you don't show the content of the potentiometer superblock. The valve input (independent of ls or not) is a signal input. In the potentiometer, you must use a potentional sensor to convert voltage into a signal (or correspondingly for current). In the valve parameters you scale the input to max input value (e. g. 10 (V) for 100 % opening).
1 -
Hi AJ,
That's interesting, can you share your model so I can have a better look and advice?
Here is two versions of the model with two different valves. Both yield similar results that are somewhat accurate but when using certain values on the potentiometer the results become very wrong and scued. Ideally I think I need a load sensing valve.
Let me know if you have any suggestions!
0 -
RoKet_21298 said:
Hi AJ,
Are you intentionally using a load-sensing valve? The ls-port (connected to pump and motor) only represents a pressure, the flow is internally not connected to port A or T. This could disturb the entire system.
I'm not sure how you want to control the motor, but typically you could use a standard directional valve (PropValve43PT2) to control speed and direction of the motor.
Unfortunately you don't show the content of the potentiometer superblock. The valve input (independent of ls or not) is a signal input. In the potentiometer, you must use a potentional sensor to convert voltage into a signal (or correspondingly for current). In the valve parameters you scale the input to max input value (e. g. 10 (V) for 100 % opening).
Ideally I would like to use a load sensing valve yes as it more accurately represents the valve I am attempting to recreate. As for the potentiometer you mentioned, I did have a signal leaving the block using the potential sensor so I don't think that is the issue. Below I have attached two versions of the model, one with an ls valve and one with the valve you suggested. I also tested using the 43LS valve and got similar results to the two that I am showing. Varying the potentiometer yields different results that somewhat portray what should happen but are not very accurate. If there is anything you can see or notice from the model please let me know as your initial suggestions were already very helpful!
When opening the model don't worry about all the graphs that pop up as they don't mean anything to the simulation. The only ones that matter are the scope block after the motor and the before and after pump pressure window that will show up.
Cheers.
0