Modeling Steel Deck Stiffness using Semi-Rigid Diaphragms in Altair S-FRAME
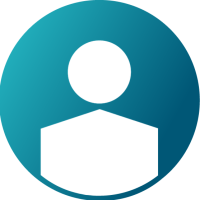

We are often asked how to represent steel decks in S-FRAME and wanted to provide a road map for those looking to do just that.
Assume we have a steel deck that we wish to analyze in S-FRAME. It is important to use accurate material properties to represent the stiffness of the steel deck. We can work with the information provided by the Steel Deck Manufacturer to help formulate the analysis model properties.
Step 1: Determine the effective material properties based on material supplier catalog data.
For the sake of this example, we assume that we are dealing with a 10m (L) x 8m (B) span with a 2.9kN/m in-plane load (q) applied on the long edge. The short edges will be pin supported. We will use Canam’s P-3606 profile (Type 22) for this example, and the Rigidity Factors (G'), thicknesses (t), and more can be found in Canam’s documentation.
We will assume a Poisson’s Ratio () of 0.3 for our steel material.
From the Canam documentation, the Rigidity Factor (G’) for our profile is taken as 2.8x103 N/mm.
With this information, we can estimate the shear deformation in our steel deck using the following equation:
To represent this steel deck in S-FRAME, we will want to apply an Effective Youngs Modulus (E’) for the diaphragm.
To determine the associated Shear Modulus we can use the following relationship between Youngs Modulus, and Shear Modulus:
Step 2: Create a new material property with the calculated values.
I have a representative S-FRAME model that is pinned on the two shorter edges, with a shell thickness of 0.76mm. We have also used a dummy member to apply the UDL to the longer edge, as shown in the image below:
We have created a modified material with the Effective Youngs Modulus of our deck. Note that it is possible to define Orthotropic Material properties, if desired.
Step 3: When ready, run the analysis with the effective material properties.
After the analysis, we can observe the deflection contours, and see that we are observing around 1.32mm of displacement in the Y-axis.
This is perhaps a surprise, as the hand calculation anticipates a deflection of approximately 1.6mm. In our experience, the underlying assumptions used in determining the deck stiffness factor require assumptions that are often on the conservative side, leading to large deflection estimates.
Note as well, that the formulas are generally based on 1D elements, so the distribution of forces, and deflections will differ when compared to a 2D element model.
If you are looking to perform Composite Steel Design, we have a separate article on this topic you can find here.