Non-Linear Optimization of Suspension link for Optimial Performance using Altair's OptiStruct and HyperWorks
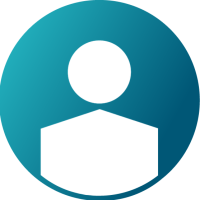
Magna Cosma and Altair Engineering have collaborated on this design exploration study using Altair OptiStruct and HyperWorks in which a representative FEA model of the suspension link was subjected to various linear and non-linear load conditions, including bushings with nonlinear stiffness properties. Links of various sizes and shapes are used in a multi-link suspension that uses three or more lateral arms, and one or more longitudinal arms. Suspension links act as a rigid connection between wheel carrier to vehicle chassis which transmits forces and displacements without delay (stiffness), without geometrical instability (buckling, permanent set), without failure (strength) and most importantly with minimum inertia (mass). Performance metrics were used as targets in a topology optimization to estimate an optimal material layout/load path and cross sections which satisfy various design constraints and objectives. Multiple manufacturing options were considered in this study to explore the most efficient design. Further fine-tuning optimizations such as size and shape optimization were run to arrive at final size and form of the design which meets all design conditions.