Simulation-Driven antenna design to meet environmental specifications
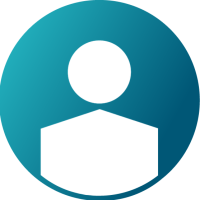

With growing communications, nowadays there are increasingly sophisticated antenna systems that are mission critical. Advances in electromagnetic (EM) simulation tools such as Altair Feko [1] have significantly improved the design process for such systems, resulting in reduced testing time and costs. To meet the system requirements, antennas are designed for factors such as return loss, gain, polarization, bandwidth etc. Once the basic structure of the antenna is designed, it is handed over to mechanical engineers to certify the ability to withstand the physical demands placed on the antenna by the environment. The ability of antennas to survive and continue to function as designed is critical for long-term deployments on various platforms such as aircrafts, ships, ground vehicles, IoT/M2M applications as well as for safety purposes. Specifically, during flight operations, antennas are routinely subjected to uncompromising operating conditions such as extremely low/high temperatures, vibrations, shock etc. to meet specifications as defined in standards such as MIL-STD 810 [2]. Normally, mechanical design of antennas is done by experience, intuition and following rules of thumb. Once a prototype is made, it is tested physically for environmental suitability at testing facilities such as [3,4], resulting in many design iterations before the antennas pass all environmental specifications. This a very expensive and time-consuming process leading to increased costs and delays in product development. In this paper, we illustrate a simulation-driven workflow process using Altair HyperWorks Suite [5] for antennas to meet environmental specifications during the design process so time taken for test and certification can be minimized and thus, cost savings and faster product development cycles.