EV Charge Controller Design
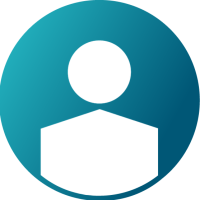

EV Charge Controller Design
Ed Wettlaufer
Senior Technical Specialist
Jacob Hammitte
Project Engineer – Mechatronics
Background – AFREECAR – Mobility and Freedom for All the World
Mobility improves quality of life by providing access to people, places, and experiences. It also enables economic advancement by providing access to goods and markets. These are considered self-evident truths here in the developed world, but can mobility also transform quality of life and economic development for the world’s poorest people, such as rural Africans?
Figure 1 - EV Cart Rendition
Imagine a solar-powered EV service that is operated and maintained by a village entrepreneur. This could address the need for many women to individually walk to collect wood from the forest (or to collect water from a well) and provide time for education or to make goods that generate income. High isolation loads in Africa can permit a low speed, lightweight vehicle to travel daily between adjacent villages. This could facilitate access to fertilizer distribution centers, to markets for crops and crafts, and to healthcare that may not exist in the village. The business is funded by users as it enables them to sell their goods. It may also be financed by government education subsidies for women and children. When not providing mobility, it could be the village’s power source for pumping water, grinding grain, and charging cellphones.
Introduction
Today’s electronics are being used to electrify everything. Shrinking in size and managing higher power; they are being pushed to their limits in every regard. Time to market constraints tighten to stay ahead of competition. Development of printed circuit board (PCB) electronics can be split into three main sections: the schematic, layout, and program. To aid in the development of a schematic, Embed with the digital power library is a useful tool. For the layout, PollEx can be used to identify any problems that may cause manufacturing difficulties or failure of components. To Program the board, Embed can be used to generate C-code which is executed on many common microcontrollers.
These three tools together can be used to fully develop electronics in a fraction of the time. It removes some need for physical tests which will reduce cost and time needed to obtain parts. Instant feedback is also acquired when using both of Embed or PollEx. This creates less time in-between iterations and designs.
For this article, the Afreecar solar charge controller will be used to demonstrate an effective process using Embed, Embed Digital Power Designer, and PollEx. Afreecar is a non-profit organization that wants to deliver mobility and power to rural countries in Africa. The main plan for Afreecar is to create a low-cost solar electric vehicle (EV) kit. This kit would accomplish the goal of bringing power and mobility to rural Africa. Along with the creation of many new businesses.
Design
A solar charge controller takes in power from a photovoltaic array and converts it into power that is safe to charge a battery. The most common way to do this is by using a voltage regulator. For the Afreecar EV a specific voltage regulator called a switch mode regulator was chosen. Switch mode power supplies come in three different common topologies:
- Buck – Decreases the voltage from input to output
- Boost – Increases the voltage from input to output
- Buck-Boost- Increases or decrease, but turns a positive voltage into a negative and negative voltage into a positive
For the solar charge controller on the Afreecar a Multiphase Buck Converter (MBC) topology was chosen because it is the most stable and allows for lower current on the input side. When designing a switch mode regulator there are many things to consider along with the topology, such as control theory, phases, and maximum voltages/currents of each side. To charge batteries safely, both constant current and constant voltage charge modes should be used.
Figure 2 - Multi-Phase Buck Converter
To start defining the specifics, the solar charge controller was modeled in Embed using the Digital Power Designer library. The MBC block from the library provides the ability to change every component inside the multi-phase buck converter to achieve specifications. The EV solar charge controller specifications required an input voltage of 54V to 96V and an output voltage of 51V at a max of 20A of current. To achieve this, a two phase buck converter operating at 200 kHz was designated. For each phase a 22uF inductor was chosen. This converter was simulated, using Embed, with both a current control mode and a voltage control mode. Both yielded exceptional results. To transfer from the Embed model to a real schematic, components were chosen that had similar functions or values to the components in the simulation. Once the schematic was created the Layout for the printed circuit board could be completed.
Figure 3 - Embed MBC Model
Verification
Set up parameters were required to properly verify the boards performance using PollEx PCB. First, using PollEx UPE, each part’s body and leads were added. Following this, properties were assigned, such as anticipated power dissipation, thermal resistance, and electrical parameters. With the properties correctly assigned, the simulations could be executed with PollEx PCB. The tests conducted included thermal analysis, signal integrity and Design for Manufacturing (DFM).
In this case, the thermal analysis was the most important of the three, because of the environment this PCB would operate in. The African climate averages about 30°C, which 5°C higher than normal room temperature. This plays a large role in the life expectancy of the components on the board. Certain components, like electrolytic capacitors, are extremely prone to failing from extended exposure to heat. By viewing the results of the thermal analysis we can see that most of the heat is surrounding the power MOSFET's. The hottest temperatures observed on this board were approximately 69.5°C, while the majority of the boards surface and components averaged 55°C.
For signal integrity, the most likely source of problems manifests from cross-talk generated by the switching power supply. Signal integrity tests verified acceptable signal fidelity. DFM analysis identifies any issues associated with manufacturing. The DFM analysis checks items such as drill size, silk screen guidelines, and pick and place assembly. The results of the DFM revealed several, easy to correct, issues with the silkscreen with all other items a “go” for manufacture.
Figure 4 - Temperature Distribution on MBC
Conclusion
The use of simulation tools can greatly decrease the time needed to design microcontrollers. Embed and PollEx provide simulation driven design, reducing the time spent in development and eliminating potential design loops. Embed enables designers to build a functional schematic with blocks and simulate their designs performance, before committing to a circuit schematic. PollEx can be used to layout and identify any printed circuit board problems through simulation. Using these tools together, the designer frontloads the design process with simulation and avoids costly errors.