Using data acquisition to drive modeling and simulation, to support the use of digital twins.
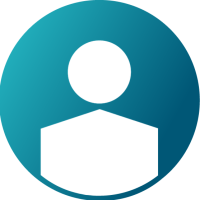

Simplifying Vehicle Road Load Collection to Drive Finite Element Structural Models
Ed Wettlaufer – Sr Technical Specialist, Altair / March 18, 2022
|
Introduction
Finite Element (FE) model boundary conditions are paramount to generating accurate results; and collecting loads on moving vehicles can be challenging and expensive. Ultimately, the Analyst is seeking the loads on the vehicle frame or structure. These can be measured directly by integrating force transducers into the vehicle suspension. These transducers are usually tailored to the application and expensive and time consuming to integrate. Strain gages are sometimes used on the vehicle structure, but their output is often difficult to validate, and the measured strains must be used to generate the boundary conditions for the structural model. Another method is to integrate wheel force transducers, also custom to the application and expensive. The wheel end forces can then be used to exercise a multi-body dynamics model to recover the forces realized on the structure. All these methods require extensive instrumentation and intermediate steps to arrive at the forces realized by the structure. The proposed alternative is to collect limited acceleration data, six to ten triaxial accelerometers depending on the number of structural modes of interest and apply those to the FE model in a Modal Transient Analysis. This method could be applied to structural models, damage models or digital twins and structural health models. The objective is to reduce the complexity of the Data Acquisition Kit (DAQ), and modeling / computer processing time.
Challenges
Accelerometer measurements exhibit trace amounts of zero drift which accumulates with time. It was initially presumed that Inertial Relief (IR) could be used to generate “balance forces” to nullify the drift, however, IR is not supported in the Modal Transient Analysis. The author was forced to signal process the accelerations and apply them as enforced displacements. Due to the drift error, integration of the signals results in significant accumulated error proportional to the duration of the signal. The author employed recursive processing over short periods of time. These methods are the foundation of filters such as the Bayesian estimation, Kalman filtering, or Hidden Markov Modeling, and provided good correlation to measured strains in the test specimen. In Kalman Filtering “The algorithm works by a two-phase process. For the prediction phase, the Kalman filter produces estimates of the current state variables, along with their uncertainties. Once the outcome of the next measurement (necessarily corrupted with some error, including random noise) is observed, these estimates are updated using a weighted average, with more weight being given to estimates with greater certainty. The algorithm is recursive. It can operate in real time, using only the present input measurements and the state calculated previously and its uncertainty matrix; no additional past information is required.” [1]
Problem Formulation
A test specimen was designed to be suitable for laboratory testing and exhibited a sufficient number of Eigen values below 350 Hz.
Figure 1 - Steel Specimen 1.38 Kg, Dimensions in mm |
Figure 2 - Specimen Eigenvalues
The specimen was fixed to linear actuators at its corners, in the test rig and excited in a random fashion, with the actuators vertically out of phase, at frequencies sweeping from zero to 10 Hz. To simplify the problem the test specimen was primarily exercised in a vertical only fashion. A real-world scenario should include all three axes at each location. The model was exercised with the measured signals, and since the strain gages are producing output based on all three directions, the model has a potential for error.
Figure 3 - Test Specimen in Test Rig
8 MEMS Accelerometers, 4 displacement transducers and 3 strain gages were fixed to the specimen and data collected for the events at a 500 Hz sampling rate. Primary and secondary modes of the structure are responsible for most of the stress. The accelerometers were positioned two on each of the four sides splitting each side into thirds. This arrangement should capture the structures primary modes. The displacement transducers were fixed at the corners co-incident with the actuators and the strain gage locations selected based on preliminary FEA results to capture those areas of highest strain. Consideration of higher order modes should require more accelerometers and further studies would be required to determine best practices.
Experiments and Results
Acceleration, displacement, and strain data was collected for several tests and compared for repeatability. Satisfied with the experimental repeatability, data was collected for the simulation.
Figure 4 - Acceleration at Location #1 Vertical Direction
The recursive filter was applied to the acceleration data and mathematically integrated to calculate velocity. The process was repeated on the velocity to obtain the displacements. These time history displacements were applied to the FE model as boundary conditions for the Modal Transient Analysis.
Figure 5 - FE Model of Test Specimen
The strains predicted in the FE analysis were plotted and compared to the strains measured from the laboratory test. The results correlated better than expected.
Figure 6 - Strain Measured v Simulated
Conclusion
The results of this experiment correlated well with the results of the computational model, suggesting recursive filtering methods could provide a means to drive FE models real time, simplifying the data collection cost and complexity. This simplified laboratory experiment re-enforces the promise of the method presented. The next step should be to test and model a structure, which has been tested and model with conventional methods and compare the results. As stated previously, there are many applicable scenarios for this technology. Instruments could be permanently installed on a structure such as a bridge and a digital twin exercised, using the acquired data, in a nearly-real-time fashion to predict the structures health, maintenance requirement and end of life predictions.
References
[1] Paul Zarchan; Howard Musoff (2000). “Fundamentals of Kalman Filtering: A Practical Approach” American Institute of Aeronautics and Astronautics, Incorporated