Realistic Road Simulation using Point Cloud Data Roads in MotionSolve
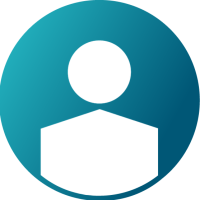

Overview
PREFACE
Physical vehicle testing is expensive and resource intensive. Vehicle modeling and simulation provide an efficient addition to the design process which can be implemented earlier in the design cycle to understand a vehicle’s dynamics. Multibody dynamics software such as Altair MotionSolve allows users to set up and analyze a wide range of dynamic systems, including vehicles. MotionSolve includes a large selection of vehicle events which allows users to analyze vehicle performance parameters. Results can be used to refine vehicle design and improve occupant comfort.
INTRODUCTION
Automotive engineers face the challenge of assessing vehicle performance under a variety of conditions before manufacturing. This can be particularly difficult when designing a vehicle to be off-road capable. However, there are solutions allowing designers and engineers to simulate vehicle performance on custom roads. Altair MotionSolve utilizes point cloud data (PCD) roads to create custom road surfaces that interact with the MF Swift tire model allowing users to predict vehicle dynamics, durability, and rider comfort. In this example, we will demonstrate the results of a pick-up truck following a path along a rough, PCD road.
Understanding the Model Definition
The PCD road requires a road surface created in any CAD package or a real-world road scanned in as a 3D model. Once a model of the road is created, use HyperMesh to create a 2D trias mesh of the road surface. Then create a road definition file and reference the road mesh fem. The MF Swift tires use the finite element mesh to determine the location of the road and ensure proper tire-road interaction. In addition to the PCD road, the model requires a path for the vehicle to follow along the road. In this case, we use a 3D curve generated from a set of points. The curve is highlighted in blue in MotionView and HyperView.
The vehicle is built using MotionView vehicle assembly tools. An assembly wizard allows the automatic creation of standard vehicle systems which can be populated with design data. The tires are provided a tire data file based on an MF Swift tire model.
After creating the road, path, and vehicle, a custom road course is created using the events tool. The road course requires the road property file and vehicle path. In this instance we use a custom velocity profile for the vehicle, but constant velocity profiles are also an option.
Pre-Requisite
SOFTWARE REQUIREMENTS
MotionView (2024 or newer)
MotionSolve (2024 or newer)
MODEL FILES
PCD_Road_Simulation.zip (See attachments)
Usage/Installation Instructions
MODEL SETUP & SIMULATION STEPS
- Open Pickup_Truck.mdl in a new MotionView session.
- Select run and choose a result directory.
- Run the motion analysis.
- Use HyperView to open the h3d result file to view the animation.
Post-Requisite
RESULTS
After running the analysis, the results can be animated in HyperView. Users can also plot and analyze key performance indicators in HyperGraph.
Pickup Truck Off-Roading Render
Pickup Truck Off-Roading Animation in HyperView
CONCLUSION
PCD roads allow users to scan real-world roads or develop 3D models in order to simulate vehicle dynamics. In combination with a vehicle assembly wizard, vehicles can be quickly built, populated with design data, and analyzed for performance. This simulation-powered-design approach lets engineers quickly evaluate different vehicle designs. Powerful post-processing makes gathering data on key performance indicators quick and easy.
AUTHORS
John Dagg, Systems Engineering Intern
Christopher Fadanelli, Solution Engineer - Systems Integration