Optistruct - large contact forces
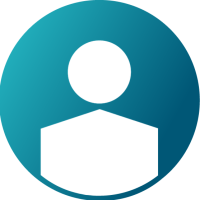
Hi All,
I seem to have a recurring issue and it doesn't seem to make much difference if I use S2S or N2S.
I have a number of very similar models, all set up the same way and I would only expect a mild difference in stress distribution and contact. What I get is with some of the loadcases I have an extremely high contact force. Now I've encountered this before and have needed to switch to gaps but this time I really do need the contact forces exported.
Here are some notes.....
NLPARA = NINC 10
PARAM = CNTSTB
Contact card = Adjust = auto, type = slide, MORIENT = Norm.
In general, slave contact surface is smaller mesh size.
<?xml version="1.0" encoding="UTF-8"?><?xml version="1.0" encoding="UTF-8"?>
I've added some images....
Answers
-
Hello Andy,
In your case, I would recommend the following for the CONTACT card:
TYPE=SLIDE
MORIENT=OPENGAP
SRCHDIS= check your distance, small value
ADJUST=NO (be carefully with AUTO, I would not take it!!)
CLEARANCE=0 (if it is a closed contact at the beginning)
DISCRETE=S2S (contact is smoother, better in general)
Try the model without friction first, if it works fine you can add friction.
Best Regards,
Mario
0 -
Cheers Mario,
Will give it a go and let you know.
Kindest regards
Andy
0