If it doesn’t have shape, then it’s probably wrong!
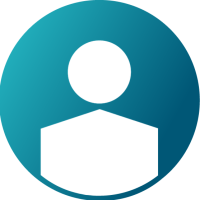

[This article was originally posted on the EDEM website blog in December 2014]
At the heart of any industrial DEM simulation is the mathematical representation of a real bulk material, which is also termed the ‘Material Model’. There are lots of aspects to a material model – the physics model used and corresponding inputs for example – but a crucial one is the shape of the particles used. DEM simulations fall into one of two categories: those that use particle shape, and those that use single sphere particles.
Single-sphere or multi-sphere? Shape should be an integral part of any industry-spec DEM simulation
The appeal of single sphere particles extends from the perception that adding shape is a computational burden. However, when shape is introduced using a multi-sphere approach, the additional computational overhead is an order of magnitude smaller when compared to other approaches such as polyhedral particles.
Choosing single-sphere particles in the belief purely on the basis that simulations will be quicker is a route that carries high risks. I have calibrated 100s of material models and in my experience particle shape is one of the most important factors in determining how a bulk material flow will behave.
There have been numerous studies in the literature since the 1990’s into shape, and each has concluded that some shape is absolutely required to stand any chance of reproducing anything that approaches realistic bulk flow behavior. Shape generates interlocking between particles and adds real resistance to shearing in a way that single spheres never could, regardless of what rolling friction physics models are used. Sacrificing shape means you risk sacrificing accuracy.
It is true that the influence of shape is also one of the harder DEM inputs to try and quantify, and “How much shape is required?” is a question often asked to me. Again, drawing on my experience, for me it is just the fact of having some shape present that will make a difference. Having ANY shape is better than no shape!
To help demonstrate all this, consider the following snapshots of a transfer chute. The image on the left shows a DEM simulation based on single sphere particles. To all intents and purposes the chute seems to be behaving in a reasonable manner. However, in the real world, this chute is carrying a fine sticky ore – is this really how you would expect it to behave?
Spot the difference! Introducing shape into simulation allows realistic material flows to be produced
With single spheres, no matter what else you do to the Material Model it is not possible to get the high repose angles and cohesive strengths that are present in the real world. Now consider the image on the right. This is the same chute, but this time shape has been introduced. The difference is staggering, and much more representative of a cohesive ore. Only with shape is it possible to make meaningful engineering decisions on the effectiveness of a design.
So, next time you are presented with some DEM results and you want to know if it is likely to be a representative reflection of the real system, the first thing you should check is whether it has shape. If not, it’s probably wrong!