Challenges of handling and processing powders Powders are a fundamental material used widely in the process industries including pharmaceutical, food, chemicals, cosmetics and additive manufacturing. Powders are involved in a range of applications from storage, transportation and delivery to processing stages such as mixing, compaction, or agglomeration. Handling and processing powder materials present unique challenges to industry because of their variable physical characteristics and flow properties. Due to their fine sizes and wide size distribution, their flow and behavioral characteristics are prone to even the smallest of variations in properties and operating conditions, such as moisture content and duration of storage. There are many challenges linked to powder handling including non-uniform mixing, segregation, caking, blockages, arching, breakage, attrition and more. These can have a strong impact on the productivity of operations and the final product quality attributes. For instance, poor powder flow can lead to blockages in a bin or hopper that might stop the production line, which will affect the efficiency of the whole operation and create health and safety issues for plant operators. An inefficient mixing process can negatively impact downstream processes such as granulation, milling and tableting. It can adversely impact product quality and result in potential batch failure and added costs due to production delays. When handling powders, process engineers and operators are also faced with many questions such as what device/design to use for a given powder, what mixing speed will help achieve a uniform blending, what is the maximum fill level possible, etc. Understanding powder behavior is critical for minimizing these problems, ensure manufacturing efficiency and avoid product quality issues. Traditionally, process engineers have had to rely on empirical methods such as physical testing to understand their systems and operations. These methods are time and labor intensive as well as expensive and they do not provide all the answers. Using simulation to better understand processes Numerical modelling tools can help understand processes better and provide key insight into operations. The Discrete Element Method (DEM) in particular has proven capabilities in capturing the complex macro-mechanical behavior of a wide range of granular solids, including powders, and to do so for a wide range of process and operational conditions. DEM is proven to be a valuable predictive tool for simulating processes in powder handling industries including powder mixing, powder conveying, spreading, milling, drying, granulation and tablet coating, to name a few. Using a DEM tool such as EDEM software means engineers can gain understanding of the mechanics of their systems beyond what is obtainable on the basis of experiments alone.
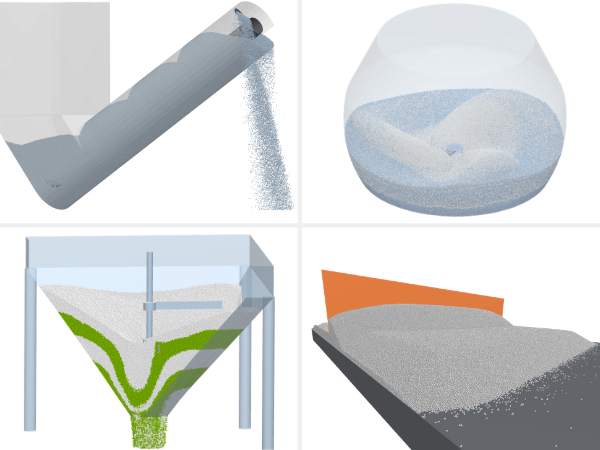
EDEM can be used to simulate a range of processes: transport in screw auger, mixing, hopper discharge, powder spreading
For instance, EDEM can be effectively used to simulate the mixing process, enabling engineers to visualize convective and diffusive flows in mixing equipment in a virtual environment. It provides fundamental information such as, the particle velocities and trajectories, and allows for the prediction of mixing and segregation rates and the identification of dead zones. This enables operators to make informed decisions on the optimal process operational parameters for their equipment, for instance regarding the impact of speed, fill level, tilt angle, etc.
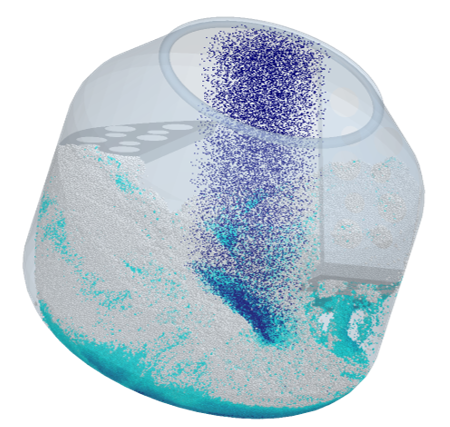
EDEM simulation of wet mixing
Another area where EDEM simulation is showing great potential is Additive Manufacturing - also known as 3D printing with applications in powder delivery, spreading, and cleaning operations. The powder spreading process for instance has a major impact on the characteristics and quality of the final product. EDEM can be used to simulate and analyze that process, providing key insights that would otherwise be impossible to obtain through experiments. It can help investigate the impact of different operational parameters such as roller speed on the quality of the powder bed as well as evaluating powder spreading uniformity, assessing the degree of compaction and visualizing the distribution of different powder layers.
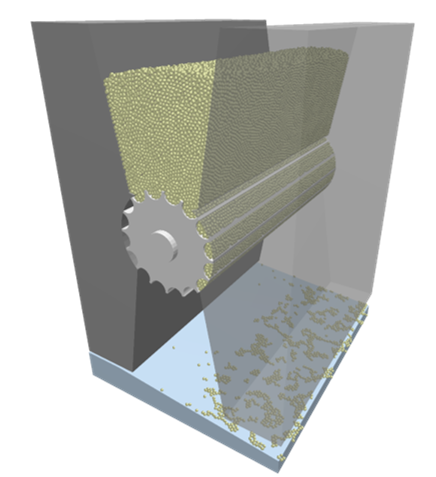
EDEM simulation of part of the delivery system of an additive manufacturing printer
When simulating powder handling processes, EDEM can help identify the root of the problem and serve as a virtual prototyping tool to test potential solutions. In addition, the fundamental insight that EDEM provides into the micro-mechanics of granular systems can be used to meet otherwise difficult challenges, such as process scale-up and the transition to continuous manufacturing. This has made EDEM an indispensable tool for optimizing process design and operation in the powder processing industries. In summary, by including Discrete Element Method simulation with EDEM in the design workflow, researchers, scientists and engineers are able to:
- Obtain a greater understanding of powder behavior
- Increase process efficiency and capability
- Optimize process configuration
- Reduce costs and dependence on physical prototyping and testing
- Drive product and process innovation
- Improve scale-up procedures
- Improve product quality
- Get products to market quicker