Over 75% of all pharmaceutical products are in the solid dosage form and particulates are involved in almost every stage of the manufacturing process. Efficient handling and processing of particulates is critical to profitable manufacture of pharmaceutical products.
A typical drug manufacturing work-stream involves several unit operations such as blending, granulation, milling and coating, all of which involve particulates in the form of powders, capsules, or tablets. Common problems areas include poor mixing, uneven coating, non-uniform die filling and pill breakage. These can have a strong impact on the productivity of operations and the final product quality. An inefficient mixing process for instance can negatively impact downstream processes such as granulation, milling and tableting. It can adversely impact product quality and result in potential batch failure and added costs due to production delays. When handling powders and particulates, process engineers and operators are also faced with many questions such as what device/design to use for a given powder, what mixing speed will help achieve a uniform blending, what is the maximum fill level possible, etc. Understanding the behavior of powders and bulk solids is critical for minimizing these problems, ensuring manufacturing efficiency and avoiding product quality issues. Traditionally, process engineers have had to rely on empirical methods such as physical testing to understand their systems and operations. These methods are time and labor intensive as well as expensive and they do not provide all the answers. Numerical modelling tools can help understand processes better and provide key insight into operations. The Discrete Element Method (DEM) in particular has proven capabilities in capturing the complex behavior of a wide range of granular solids and to do so for a wide range of process and operational conditions. DEM is proven to be a valuable predictive tool for simulating pharmaceutical manufacturing processes including powder mixing, tablet coating, die filling, granulation, milling and more. Using a DEM tool such as Altair EDEM software means engineers can gain understanding of the mechanics of their systems beyond what is obtainable on the basis of experiments alone. 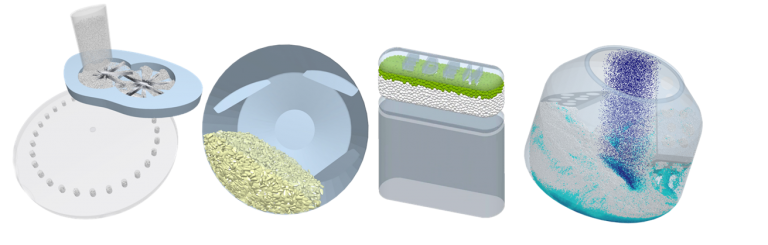
Altair EDEM can be used to simulate a range of processes: die filling, tablet coating, tabletting
For instance, EDEM can be effectively used to simulate the mixing process of powders and tablets. It provides fundamental information such as the particle velocities and trajectories and allows for the prediction of mixing and segregation rates as well as the identification of dead zones. This enables operators to make informed decisions on the optimal process operational parameters for their equipment regarding the impact of speed, fill level, tilt angle, etc., and to assess mixing efficiency. 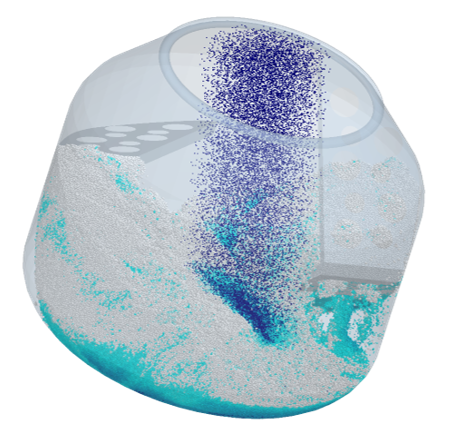
EDEM simulation of wet mixing
Another example is coating. Coating uniformity is of critical importance for the tablet-coating process. With EDEM it is possible to obtain key parameters such as the residence time of the tablets under the coating spray, intra-tablet coating variability, and tablets velocities pattern - many of these are difficult or even impossible to get by experimentation. EDEM can also be used to investigate how the shape of a tablet, the drum's speed, and the fill level are influencing the coating process.
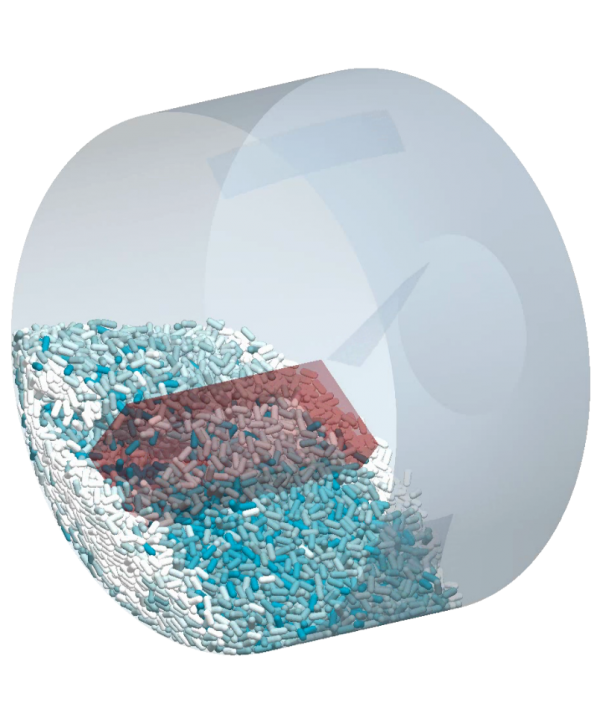
EDEM simulation of tablet coating
When simulating pharmaceutical manufacturing processes, EDEM can help identify the root of the problem and serve as a virtual prototyping tool to test potential solutions. In addition, the fundamental insight that EDEM provides into the micro-mechanics of granular systems can be used to meet otherwise difficult challenges, such as process scale-up and the transition to continuous manufacturing. This has made EDEM an indispensable tool for optimizing process design and operation in the pharmaceutical industry. In summary, by including Discrete Element Method simulation with EDEM in the design workflow, researchers, scientists and engineers are able to:
- Obtain a greater understanding of powder behavior
- Increase process efficiency and capability
- Reduce costs and dependence on physical prototyping and testing
- Drive product and process innovation
- Improve scale-up procedures
- Improve product quality
- Get products to market quicker