Altair® Flux® 2024 Release Highlights
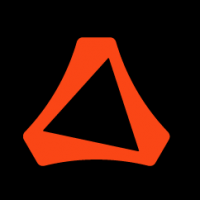

Let’s have a look at the key features and improvements of Altair® Flux® 2024
With always more pressure on reducing the time to deliver new products, designers need to be efficient when exectuing simulation tasks. The most precious time is the one you spend to enter and post-process models, but solving times are also important. Conscious of this, the Altair Flux team is providing in the 2024 version new capabilities and automations in the SimLab environment allowing to reduce pre-processing efforts. Many improvements are also brought to reduce the time you need to get your results.
TIME GAINS IN MODEL SET-UP
Meshing plays an essential role in getting good results and providing the best solver performance. This is key when you want to evaluate eddy currents in solid conductors in 3D, but it may take time to define. SimLab is now offering the capbility to easily establish a “skin depth mesh” in conductors, allowing to get an optimized mesh of complex geometries in just a few clicks. Other meshing tools have been improved to deal with symetries and periodicities, to check mesh quality and to mesh the air “infinite” region.
Getting an efficient 3D mesh for eddy currents computations in a few clicks
When modeling a motor in 3D, one challenge is to deal with the modeling of the windings. One key feature of Flux is to use non-meshed coils that will reduce the mesh size and solving times while keeping great accuracy. A new automation procedure is proposed in SimLab to build them directly from a CAD import. Another example of automation is the creation of the electric circuit corresponding to a given winding configuration. That’s a lot of time saved when defining a machine with a hairpin winding type.
EFFICIENT 3D EDDY CURRENT MODELING
For applications like induction machines or transformers, the use of frequency domain simulations instead of transient is a big gain of simulation time. Steady-state AC analysis is now available from SimLab in 3D with all the benefits of a powerful and intuitive user interface.
3D Steady-state AC analysis in the SimLab interface
When you need to deal with power busbars, SimLab also includes a specific module based on the PEEC method that will enable the computation of eddy currents in the bars without any air mesh. The external electric circuit that connects to the busbar can be easily defined within the same interface, and joule losses in the bars can be computed for various frequencies in a very fast and precise way.
Fast computation of losses in power busbars supplied with AC current.
CONSTANT ACCELERATION OF COMPUTATIONS
Models tend to grow in size and constant rework of internal algorithms are done to maintain the best performance of Flux. In the 2024 version, new non-linear convergence criteria have been introduced to avoid unnecessary iterations and accelerate the solving of some models with low convergence rates.
Computing the losses in a skewed machine considering only half cycle. Two times faster than full cycle, same results.
Better management of the parametric distribution has also been introduced allowing for significant time gains. On a specific user case with 40,000+ time-steps, time has been cut by half. Other algorithms like the creation of electric cuts or the automated check of physics definition have also been optimized. In Flux Electric Machine Toolbox (FeMT), the computation of iron losses can now be done using only half period of signals, which in most cases will divide the computation times by almost two, with the same quality for the end results.
MODELING MORE WITH MULTIPHYSICS
One of the key advantages of SimLab is its ability to provide multiphysics anaylsis in a single user interface. The coupling between Flux and Altair’s CFD solver AcuSolve is made easy thanks to a simplified workflow that will let you map losses, usually computed in 2D, to a 3D thermal model.
Another new multiphysics capability is the mapping of structural stresses, that you have computed with OptiStruct for example, into a Flux model. In cases where this stress is localized on the edges (for example when simulating punching of iron sheets), we have introduced in earlier version line approximations, but for other situations where the distribution of the stress spreads into the material, you need to get a complete mapping in space to evaluate the impact of the stress on magnetic performances.
AND ALSO:
- Easy move from a 2D model to a Skew model
- Loss Surface model : Two new electrical steel grades added (NO25 and M250-50A)
- Improved macro for FluxMotor part creation
- New application example for Wound Field Machine modeling
Discover these improvements in more detail by looking at the Release Notes of Altair® Flux® 2024
You can also find the full documentation online:
Altair® Flux® can be downloaded on the Altair One Marketplace (with your account) here.
Enjoy Altair® Flux® 2024 version!
If you want to know more about Altair® FluxMotor® and its new features, look at the Release Notes.
Yann Le Floch - VP – Program Manager Flux®
Vincent Leconte - Senior Director Electrification Solutions
Comments
-
For using Flux in SimLab, are we able to simulate the application of Steady State AC Magnetic coupled with Transient Thermal 3D?
- Jerome.
0 -
Jerome Teoh said:
For using Flux in SimLab, are we able to simulate the application of Steady State AC Magnetic coupled with Transient Thermal 3D?
- Jerome.
Hi Jerome,
We are working on it. It should be available in the next version.
Yann
1