Volvo Cars: A DEM study to investigate the influence of ice particle cohesion on the angle of repose
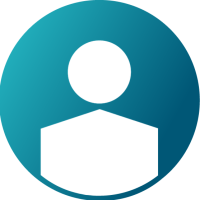

Contamination on road vehicle surfaces is not an uncommon phenomenon and often occurs in harsh weather conditions. It may come in various forms like dust, snow, stone chipping, water etc., with each of them responsible for one or several negative effects on a car. Contamination of snow most often occurs in cold regions when a car is driven on a snowy road and the tires lift snow while driving (Figure 1). Snow, which is a granular material consisting of ice particles is a sticky material where the cohesion is very temperature dependent and tends to accumulate on surfaces. For road vehicles this accumulation of snow can reduce or even block the availability of sensors on a vehicle such as cameras, radars and lidars and thereby reduce the functionality of active safety systems that are dependent on these sensors. This problem with sensor blockage will be even more problematic for future cars with autonomous functionalities since the vehicle then is fully dependent on sensor availability.
Figure 1 - An example of snow contamination on a Volvo V90 where snow is lifted from the ground by the tires while driving.
Volvo Cars has a long history of working with Computer-Aided Engineering such as Computational Fluid Dynamics (CFD) in early stages of development. Using CFD combined with Lagrangian particle-tracking, simulations of snow accumulation on a vehicle surface can be done to predict where snow will stick on a new design. Identifying snow impingement on active safety sensors in an early design stage accelerates the development of increased sensor availability. However, to accurately predict snow accumulation at various temperatures and for different snow types, the cohesive properties of ice need to be better understood. This can be done by observations of more simple experiments on snow and/or ice.
A micro-mechanical property of a granular material is the angle of repose, which is the steepest angle of descent relative to the horizontal plane to which a granular material can be piled. Experimental measurements on the angle of repose of snow was carried in northern Sweden by Volvo Cars in a research project. As the snow is a cohesive material, the traditional way of evaluating angle of repose is not suitable for ice particles. Instead, the experimental setup consisted of a platform and the sieve shaker from which the ice particles fall onto the platform and accumulate, forming a cone. The experimental setup is shown in Figure 2. When there is no further growth of the cone, the angle of repose was measured. The experiments were repeated at different temperatures and snow types. The measurements show a very high sensitivity to temperature where the angle of repose is increasing with increased temperature.
Figure 2 - Experimental setup to measure angle of repose at different temperatures.
The experiments were replicated virtually using the Discrete Element Method (DEM) in a collaboration between Volvo Cars and Altair. The software EDEM was used to simulate the angle of repose for snow where ice particles were simulated to fall in air towards a cylindrical platform. Particles trajectories and velocity were calculated using gravitational forces and drag forces exerted on the particles. The Johnson, Kendall, Roberts (JKR) model was used as contact model for the particle-particle and particle-wall collisions. The JKR model from EDEM is suitable for the ice particles that have Van der Waals attraction forces when they are in contact with each other and has been used before to simulate ice particle collisions [1]. In this model the work of adhesion, Γ, is the material property that defines the cohesion/adhesion in an interaction. Based on the experimental results, this property is predicted for ice particles to be temperature dependent for temperatures close to the melting point of water. By varying Γ and correlating the obtained angle of repose with the experiments the relationship between Γ and temperature can be obtained.
The particle properties were defined according to the particle size distributions obtained from microscope samples of the experimental measurements. EDEM also enables the user to create non-spherical particles (Figure 3) by grouping several particles which behave as a single particle i.e., having same material properties and move with same velocity.
Figure 3 - Non-spherical particle in EDEM
The particle sizes in these simulations varied from 200 µm to 400 µm in radius. Solving the JKR contact force for a large number of such small particles and a large number of particle-particle contacts causes a large computational cost. EDEM has a sophisticated method called “dynamic domain” where, particles having minimal movement outside the pre-defined dynamic domain will be frozen and no contact forces are calculated on those particles thereby reducing computational cost (Figure 4). In our case, the ice particles being in a pile for a while will undergo a phenomenon called “sintering” and stick together. This has been an additional advantage for us using the dynamic domain. The simulations were also performed on GPU processors to further speed up the simulation time.
Figure 4 - Dynamic domain from EDEM used to mimic sintering phenomenon of ice particles.
The angle of repose for varying Γ is shown in Figure 5. The results from the simulations could be matched well with the experimental trends and acts as a validation of the used material properties for ice particles. Figure 6 shows a comparison between simulation results with Γ = 0.218 J/m2 and experimental results at T = -12°C.
Figure 5 - Change in angle of repose with change in work of adhesion (Γ) value.
Figure 6 – The angle of repose for snow comparing a simulation result using Γ = 0.218 J/m2 with an experimental result for T = -12 °C.
The goal of this work was to explore to what extent EDEM simulation would be able to replicate the build-up of snow. Through the activities outlined above it was possible to demonstrate that EDEM was able to provide a good match for snow behaviours using the built-in modelling and physics capabilities. This article represents a snapshot of those findings, and a summary of the overall work has been published in [2].
About the Authors
Yeswanth Sai Tanneru
Yeswanth is mechanical engineer that recently finished his master program at Chalmers University of Technology. His studies have been in fluid dynamics, turbomachines & multiphase flows.
Tobias Eidevåg
Tobias is a research engineer at Volvo Cars and an industrial PhD student. His research focus on snow accumulation on exterior vehicle surfaces and the aim is to develop numerical techniques such that snow accumulation can be predicted on sensitive exterior surfaces such as radars, camera lenses and lidars.
David Kallin
David is an analysis engineer at Volvo Cars working primarily with numerical analysis in the team Contamination & CFD.
References
[1] T. Eidevåg, P. Abrahamsson, M. Eng, and A. Rasmuson, “Modeling of dry snow adhesion during normal impact with surfaces,” Powder Technol., vol. 361, pp. 1081–1092, 2019, doi: 10.1016/j.powtec.2019.10.085.
[2] Y. S. A. I. Tanneru, “Snow Contamination on Cars,” Master thesis, Chalmers University of Technology, 2020.