Predicting Drill Wear using the Discrete Element Method
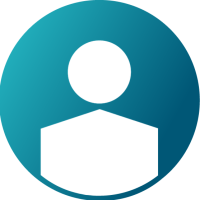
Nowadays, underground structures play a vital role in the development of various countries. These structures are constructed as part of many civil activities, such as the development of road and railways, tunnels, underground subways, gas and sewage lines, fuel storage, military installations and more. Drilling is a key operation in the design and construction of such projects. But it is not only tunnelling that characterizes our era. Overpopulation and extensive industrial activities are the driving forces leading to continuous demand for energy. In the quest for more hydrocarbons, drilling has extended to both deep water areas and to very deep wells. In these extreme conditions, varying temperatures (1-200oC) and high pressures (more than 1.000 bars) are frequently encountered leading to operation adversities and significant equipment wear (H. Rafezi, McGill University).
Being able to model drilling problems and accurately predict the wear of the drilling tools is of high importance and a challenging computational task. The wear results in considerable changes of the shape of the drilling tools which has a direct effect on the overall efficiency of excavation works. Firstly, because of its adverse effect on cutting forces, excavation rate and energy consumption, and secondly, due to the costs and delays incurred by replacements of the worn-out tools. Therefore, being able to accurately predict wear is an important element in the design and optimization of cutting tools.
Drilling rig
The Discrete Element Method (DEM) is commonly regarded as a suitable tool used in soil and rock mechanics to describe the mechanical behavior of granular materials and geomaterials. DEM can be used to investigate a range of applications at the particle scale -including drilling processes- and to monitor the interaction between materials and equipment in detail. The latter is of great importance in industrial applications as one of the basic problems in drilling is the tool wear and this depends on both mechanical and thermal effects in the tool–rock interaction. More specifically, high temperatures developed on the tool surface due to heat generated by friction between tool and rock reduce the hardness of the surface and increase adhesive and abrasive wear. Using a DEM tool provides the ability to model such processes and identify the regions in which wear is taking place.
Example case: DEM simulation of Tricone drilling operation. Provided by Dr. Nima Gharib (McGill University, Canada)
Drilling and blasting are important preliminary tasks in surface mining, where Tricone bits are preferred in most rotary applications for blasthole drilling. During the comminution process the bit is subjected to changes, known as bit wear, due to the contact between bit teeth ground formations. The bit wear will affect the drill performance significantly, therefore it is vital to be aware of the bit wear condition in drilling process in order to achieve optimal drilling performance. To address these issues, a numerical model was developed to simulate the bit wear in rock and bit interaction. The model was aimed to simulate the gradual wear of bit inserts and the rate of penetration in contact with various rock formations.
Simulation of Tricone rotary drill bit showing regions of wear (color shows depth of wear)
The Tricone drilling process was modeled using EDEM software, a cutting edge discrete element modeling package. The software was uniquely modified and optimized to simulate the drilling process which includes both the bit and the ground. Simulation of the drilling gave the applied forces on the drill body and the cones, vibration, penetration rate and the drill wear.
Simulation of Tricone drilling operation – Bit wear monitoring
Ground modeling simultaneously provided information about rock types, stratification, inclination angle and required energy for specified drilling conditions. Different rock types were defined which made it possible to estimate the bit’s life time in different working conditions.
The outcomes of this research will support a bit wear monitoring system in the next phases of the project. Such insight is directly applicable in bit manufacturing as it allows investigation and enhancement of product performance.
The following video shows a DEM simulation of a tricone drilling operation using EDEM: bit wear monitoring and layered rocks.
Comments
-
What software is this coupled with edem?
0 -
Hi Xixihaha,
I do not know exactly the software used for the above examples, but this can be doable using Multi body dynamics software such as Motion Solve, which is Altair own Multi body dynamic solver.
If you're not interested in any joint forces and relative motions, then the motion can be reproduced in EDEM as well.
Thanks,
Prasad A
0