Shielding Effectiveness of an Enclosure for a Battery Pack PCB
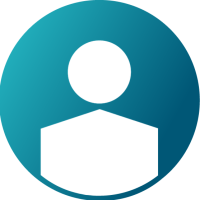
Electromagnetic shielding is necessary to protect certain RF components from external electromagnetic signals or for preventing a strong RF signal from leaking out interfering with other electronics in the system. Shielding can be used locally or globally on a PCB depending on the application of intend. For example, a casing can be used for a particular active component such as a microchip or the entire PCB with all the active and passive components along with the connectors and cables. A proper design of such casing that is immune to leakage is necessary for realizing a good RF system level design. The qualitative parameter that defines the characteristics of a good casing is termed as shielding effectiveness. It is defined as the ratio of the magnitude of the incident electric field to the magnitude of the transmitted electric field as shown in (1).
where,
There are several factors that should be considered while choosing the type of the enclosure for achieving an effective shield. They are:
- Frequency of operation.
- Electric properties of the enclosure (dielectric constant, loss tangent, and conductivity).
- Distance from the radiating source to the shield.
- Need for the presence of apertures or gaps in the enclosure for connectivity purposes.
- Thickness of the enclosure.
- Type of external or internal radiating source.
A wide variety of metals are commonly used for shielding the spurious signals and typically the PCB is covered by a plastic casing coated with metal such as copper, nickel, silver etc.
The goal of this work is to show a well-established workflow using Altair products such as Altair Feko and Altair PollEx to effectively design a good shield for a PCB. For example, consider a battery pack PCB as shown in Fig 1 as a candidate for shielding using an enclosure. The workflow is split into two procedures, one is to obtain the solution coefficient file for the traces that are radiating from Altair Pollex, and second is to use that as an equivalent source to design the enclosure in Altair Feko.
Fig 1. An example battery pack PCB that has current traces that radiates at 1 GHz.
Procedure 1: Obtaining the solution coefficient file from Altair PollEx
Step 1: Import the PCB layout with the traces and components.
Step 2: Choose the frequency at which the surface trace currents should be computed.
Step 3: Choose the two longest traces in this PCB for which the currents are computed for the given excitation.
Step 4: Export the currents in radiative emissions (.rei file) format. (see attached PCB_Current.rei)
Procedure 2: Simulating the enclosure shielding effectiveness using Altair Feko.
Step 1: Import the .rei file from PollEx and convert it into a solution coefficient (.sol) file. (see attached PCB_Sol.sol)
Step 2: Use the solution coefficient equivalent source to represent the PCB.
Step 3: Design the enclosure around the PCB as shown in Fig 2.
Fig 2. PCB represented by an equivalent source surrounded by an enclosure.
Step 4: Compute the nearfields along the boundary of the enclosure using Cartesian boundary request in Feko to compute the shielding effectiveness as shown in Fig 3.
Fig 3. Nearfields computed across the cross section of the PCB with casing.
To understand the effectiveness of the enclosure, several different simulations were performed with varying thickness of metallic coating on the outer walls of the enclosure. The results are plotted along the horizontal and vertical cross section of the PCB enclosure boundary. Fig 4 shows the change in electric field strength along the z-axis (vertical axis) outside the enclosure and Fig 5 shows the change in electric field strength along the y-axis (horizontal axis) outside the enclosure due to varying thickness of metallic coating. It can be inferred that as the thickness of the coating increases, the shielding improves. (see attached PCB_shielding.cfx).
Fig 4. Electric field strength along the vertical boundary of the enclosure.
Fig 5. Electric field strength along the horizontal boundary of the enclosure.