Altair Inspire® Challenge #3: 3D printed Structural Steel Connection Design
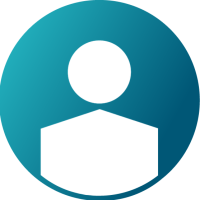

Structural Steel Connections often require carefully designed components to safely transfer loads to the ground. In this challenge we will design a 3D Printed Structural Steel Connector to transfer loads between a set of structural steel members to the ground. The design must be such that it can accommodate bolted or welded connections to connect to the Structural Steel Components, and the goal of the design is to minimize weight while ensuring the load transfer to the ground occurs without plastic deformation. The attached STMOD file can be a starting point. It contains a sample design space, loads, and supports. Feel free to adjust the design space, and optimization settings (lattice optimization) to your preferences.
Level: Medium
Product Required: Inspire
The solution can be attached in the comment section of this post. The desired output format is a JPG or PNG showing your optimized design.
The solution to Challenge "Cycling Shoe Cleat Design" can be found Here
If you would like to solve more challenges and get regular challenge release updates, Subscribe to the Altair Community Challenge forum
Comments
-
So I run couple of tests.
and I got some kind of idea what to do.
So I made first prototype, but there was still room to remove some stuff.
So I made other version:
This one looks more doable in real world. But it is do light and it can bend too much. Where the first one can bend 0,633 mm, the second one can bend 1,2 mm which is a lot.
The weight of the objects are v1: 226 kg and v2: 185 kg. So the first one must be better version.
1 -
Karli said:
So I run couple of tests.
and I got some kind of idea what to do.
So I made first prototype, but there was still room to remove some stuff.
So I made other version:
This one looks more doable in real world. But it is do light and it can bend too much. Where the first one can bend 0,633 mm, the second one can bend 1,2 mm which is a lot.
The weight of the objects are v1: 226 kg and v2: 185 kg. So the first one must be better version.
Very nice, Karli!
0 -
-
Sourav Das_20575 said:
Great work, Sourav!
0 -
Hello,
Structural steel connections play a critical role in bearing and transferring substantial loads between beams and columns. Therefore, in the process of optimization, it is imperative to execute meticulous material removal to ensure that stress and displacement remain within acceptable limits.
The original values for mass, stress, and displacement were as follows: 1108.807 kg, 14.74 MPa, and 0.7679 mm, respectively.
Through optimization, these parameters have been significantly improved, resulting in reduced values of 125.121 kg for mass, 18.15 MPa for stress, and 0.7721 mm for displacement.
It is worth noting that the connections offer flexibility in terms of assembly methods, including spot welds, line welds, or bolts. In this specific task, spot welds were employed, resulting in a total mass of 511.109 kilograms.
For the structural analysis performed after optimization, spot welds were not utilized due to constraints within Optistruct, making it necessary to exclude them from the analysis.
Thank You.
1 -
Kunal Pandit_21294 said:
Hello,
Structural steel connections play a critical role in bearing and transferring substantial loads between beams and columns. Therefore, in the process of optimization, it is imperative to execute meticulous material removal to ensure that stress and displacement remain within acceptable limits.
The original values for mass, stress, and displacement were as follows: 1108.807 kg, 14.74 MPa, and 0.7679 mm, respectively.
Through optimization, these parameters have been significantly improved, resulting in reduced values of 125.121 kg for mass, 18.15 MPa for stress, and 0.7721 mm for displacement.
It is worth noting that the connections offer flexibility in terms of assembly methods, including spot welds, line welds, or bolts. In this specific task, spot welds were employed, resulting in a total mass of 511.109 kilograms.
For the structural analysis performed after optimization, spot welds were not utilized due to constraints within Optistruct, making it necessary to exclude them from the analysis.
Thank You.
Very nicely done, and a lot of practical considerations were made. Nice work!
0 -
Matthew Sauer_21269 said:
Thanks, Matthew
0 -
Matthew Sauer_21269 said:
Thank you so much, Matthew!
0