Topology Optimization for a Housing Reinforcement to Improve Manufacturability
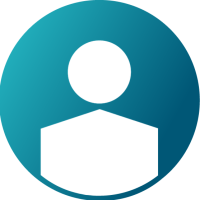
Product = GENESIS
Introduction to Housing Structures
Housing structures are used to contain and protect mechanical machinery or structural components, such as transmission boxes. They prevent the interior mechanism from being affected by outside debris and may also include integrated fittings or brackets to secure internal components. Sometimes, the housing itself serves as the body of the device, essential to its function. Adding ribs to strengthen housing structures or reduce their mass is a common practice. However, determining the optimal placement and dimensions of these reinforcements can be challenging. In this blog post, we will showcase an example of one of several methods available in the GENESIS software to solve this problem.
Example of Using Topology Optimization to Find Optimal Housing Structure Reinforcement:
In this example, the objective function is to minimize the internal strain energy to create a stiff structure while using up to 33% of additional material.
Figure 1 illustrates the housing structure to be designed.
Figure 1
The design space consists of the added volume of material surrounding the structure. Figure 2 presents the added material within the design space.
Figure 2
Topology Optimization Results
Figure 3 displays the final topology results obtained by applying one fabrication constraint. This constraint allows the ribs to grow perpendicular to the outer surface for reinforcement.
Figure 3
Figure 3 showcases the final topology results, with the ribs growing normally on the red surface while adhering to the imposed fabrication constraint. However, the ribs in this design turn out to be too tall. This issue arises due to the large designable region. Instead of altering the designable space, we can introduce another fabrication constraint to prevent the development of excessively tall ribs. GENESIS offers a constraint called "Maximum Fill Depth" for this purpose. By utilizing this constraint, we can limit the rib growth to be less than or equal to 30 mm.
Topology Optimization Results Using Max Fill Depth (Max Rib Height) constraints
Figure 4 displays the final topology results achieved by incorporating two fabrication constraints. The first constraint allows the ribs to grow normally, perpendicular to the outer surface, as in the previous case. The second constraint restricts the rib height to prevent excessive growth.
Figure 4
Figure 4 presents the final topology results, demonstrating the main ribs growing normally on the red surface while respecting the two fabrication constraints. Another requirement that can be introduced is the "Minimum Fill Depth." In the subsequent run, we will incorporate the Minimum Fill Depth constraint.
Topology Optimization Results Using Max and Min Fill Depth fabrication constraints
Figure 5 exhibits the final topology results obtained by employing three fabrication constraints. The first two constraints are similar to the previous case, allowing the ribs to grow normally and restricting their height. The third constraint enforces a minimum depth fill of 8 mm, ensuring rib growth within the specified range.
Figure 5
Figure 5 showcases the final topology results, with the ribs growing perpendicular to the housing surface while adhering to the fabrication constraints and the specified minimum and maximum fill depth.
Summary and Concluding Remarks
The GENESIS software proves to be an effective tool for designing ribs. In the presented example, ribs were designed using the normal-to-surface filling fabrication constraint and two depth control constraints. Setting up the problem using Design Studio only requires a few simple steps.
Figure 6
Figure 6 illustrates the results of three independent topology optimization runs, highlighting the impact of using or not using fill depth constraints to limit or force rib growth. To learn more about this type of problem, users can study the step-by-step example manual in Design Studio, specifically example TPDSG049. It provides a comprehensive exploration of the problem and its solutions. If you have any further questions or need additional information, please feel free to contact us. If you don't currently have access to GENESIS and/or Design Studio, we can provide more details about this specific problem or assist you in obtaining our software. You can reach us by leaving a comment below.