Product = GTAM/GSAM
Topography optimization is a special form of shape optimization which generates bead patterns or shape profiles on given design surfaces. In GSAM, the surface could come from a shell body or solid body. With topography optimization, the stiffness, frequency, or other performance targets could be optimized. In traditional shape design, you need to define the perturbation for mesh nodes or control nodes of the shape morphing domain. While in topography design, the software will automatically create the perturbation (normal to surface by default) to modify the shape of the structure. For the bracket below, we would like to use topography optimization to maximize the stiffness of the structure, and minimize the mass at the same time. The bracket is fixed at the top bolt holes and has force applied on the bottom bolt hole. 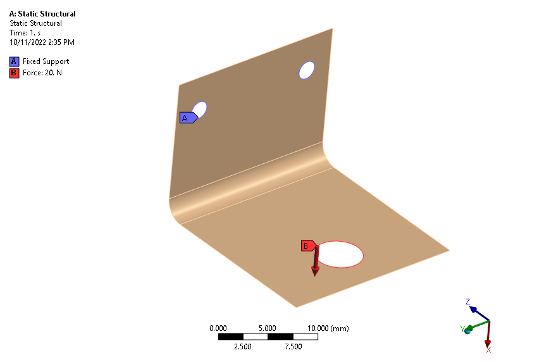
The topography region (blue) is defined over the entire surfaces of the model. The edges of the surface are also designed except the three bolt edges (green) where boundary condition and load are applied. 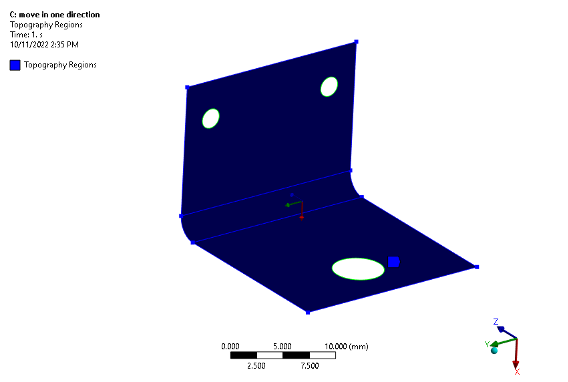
The details of topography region definition are displayed in the following image. We use a cone shape perturbation with a maximum allowable perturbation magnitude of 1.0 mm.
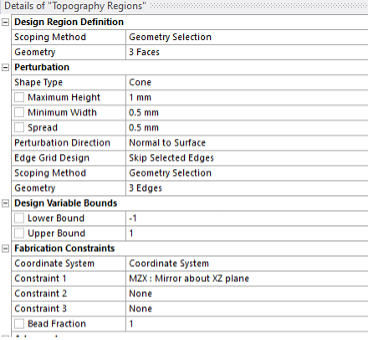
We run the topography optimization with three different cases. In the first case, we allow the perturbation to go in both directions along the norm of the surfaces. In second and third cases, the perturbation only goes along the negative norm of the surfaces. In the third case, a bead fraction of 0.3 is applied as well. With bead fraction constraints as 0.3, only 30% of nodes on the surface will be moved out of the original locations.
| Case 1 | Case 2 | Case 3 |
Perturbation direction | Normal to surface | Normal to surface | Normal to surface |
Design variable bounds | (-1, 1) | (-1,0) | (-1,0) |
Bead fraction | 1.0 | 1.0 | 0.3 |
Stiffness Change | +74.1% | +45.4% | +50.1% |
Mass Change | +7.3% | -0.5% | 0.0% |
The shape change results for the three cases are shown in the images below. The undeformed wireframe (black) of the original structure is shown for comparison. The first case has the most design freedom. By moving nodes in two directions, it gives a higher percentage of improvement for stiffness, but also increases the mass. The second case and the third cases yield similar improvement for stiffness, but the third case has more sharp beads by constraining only 30% of the nodes to move.
Case 1:
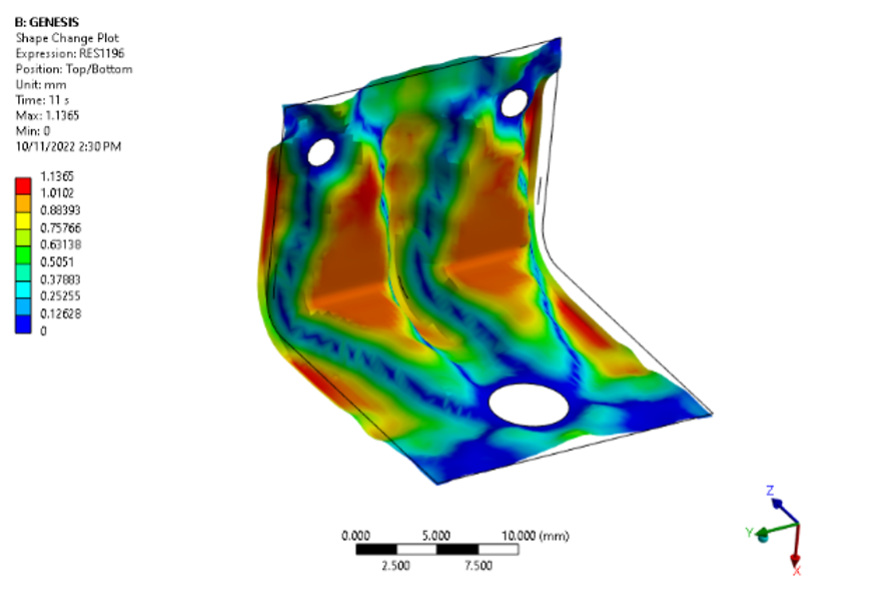
Case 2:
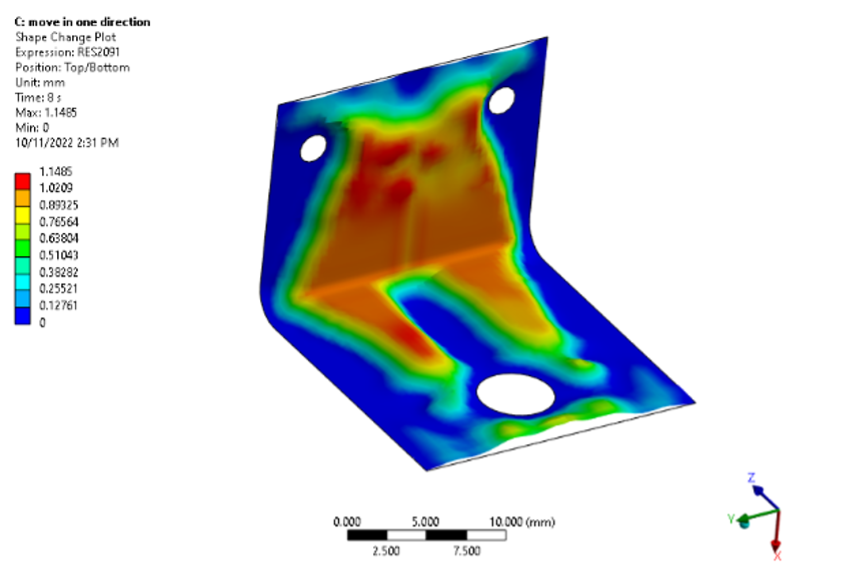
Case 3:
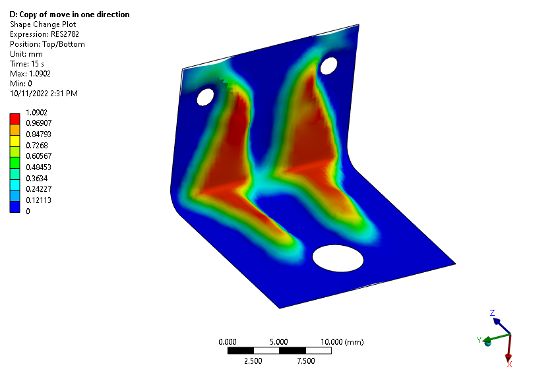
Topography optimization is a great tool in GSAM, which is easy to set up but also very useful for design improvement. For more details, please leave a comment below.
Connect with us now for complimentary webinars and evaluation software.
Our engineering team can work with you to conduct a Test Case showing how Genesis will improve your designs, processes and your overall business.