What's New in nanoFluidX 2022.0
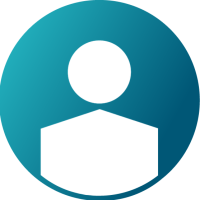
What is new in the nanoFluidX solver:
Direct Heat Transfer Coefficient output:
Previously, nanoFluidX exported its entire time-averaged flow field into AcuSolve where the thermal solver was executed to get the quasi-steady-state temperatures. This approach had limitations, so the option to export time-averaged heat transfer coefficients (HTC) directly on the geometry has been added. This approach makes Thermal Analysis more convenient, provides greater flexibility in the choice of the thermal solver, and significantly improves the overall turn-around time of the process. This feature is also greatly helped by SimLab’s existing capability to map data from one mesh to another and apply that to a thermal simulation (e.g. in OptiStruct).
Schematic process of HTC mapping: 1 – exported text file from nanoFluidX containing HTC data on the geometry; 2 – Mapping process in SimLab and running OptiStruct; 3 – Temperature field resulting from the OptiStruct thermal simulation, using nanoFluidX exported HTC values as boundary conditions.
Improvements of the impose region capabilities:
Impose regions have wide application in nanoFluidX simulations - controlling temperature, porosity, acceleration, and velocity within those volumes. The 2022 version of nanoFluidX introduces a number of improvements providing more flexibility than ever, while deprecating some of the old commands and outdated features. The regions now have more consistent behaviour and allow for more detailed control over the parameters inside the regions.
===========================================================
===========================================================
Improvements to the Simlab’s nanoFluidX Solution UI:
Significant improvements have been made to the overall workflow for nanoFluidX in Simlab 2022.
Water wading solution UI:
There is a completely new solution for vehicle wading. You can now set up water wading simulations in record time. Aside from the smooth workflow and ability to handle full vehicle geometry, it is possible to set up two frames of reference for the vehicle – a static frame and a sliding frame, depending on the desired outcome. The static frame keeps the car body fixed and can simulate only a flat road and it is suitable for higher speed simulations. The sliding frame counterpart keeps the road static and the car moving, allowing for the possibility of vertical vehicle motion and simulation of various channel depths in a single run.
We see the static frame case on the left and the sliding frame case on the right. The static frame is intended for cases where transient moment of water ingress and egress is not of critical importance; thus the simulation can be simplified and made more computationally efficient. In the sliding frame, the vehicle moves into the water, diving the front bumper first. The sliding frame generates the channel domain on the fly, inside the solver, therefore optimizing the performance.
Improved resolution definition:
Previously, particle resolution (dx) had to be defined in various locations, but now the user is asked to define the resolution only once. Aside from removing the room for user errors, this improvement has other benefits for the workflow, such as easier exploration of other resolution scenarios.
Image showing how the initial definition of the particle pitch (dx) in the solution menu propagates through the solution. This feature minimizes the room for user errors and allows for greater flexibility if various resolutions need to be explored quickly.
Parametric boundary conditions:
Parametric boundary conditions have been available in SimLab for some time, but are now fully available for the nanoFluidX solutions too. This implies easier exploration of various operational points, as you can now parametrically define the gear ratios and other motions. The same principles can be applied to all the boundary conditions in the solution.
Data check in SimLab:
SimLab now incorporates the tool for checking the setup of a nanoFluidX simulation. Once started, SimLab will provide you with a report (nanoFluidX header format) in the window stating the summary of the case and pointing out any errors it may run into or approving the run setup.
Output report of the simulation proof run inside of SimLab 2022.
Working with multiple solutions:
All of the above workflow improvements really lead into the ability to simultaneously work with multiple simulation scenarios. Making full use of the new capabilities in the workflow allows for significantly improved productivity and flexibility of the engineer in charge of running nanoFluidX.
If you would like to know more or give the new version a test ride, please feel free to contact your closest Altair representative.
#onlyforward